1. Introduction
The present work describes an implementation of laser heat treatment for the softening of 6000 series aluminum alloys. In this implementation, the study is intended to allow for improvements in cold forming through stress redistribution in the part. A localized reduction in yield stress will allow for stress redistribution during the forming process that, if executed in adequate areas, can reduce the risk of failure and fracture. Therefore, the aim of the so-called Tailor Heat Treated Blanks (THTB) is to improve the formability of the products[1], which is of particular importance for aluminum alloys due to their low formability at ambient temperatures.
Research and development efforts have been concentrated on precipitation- hardened aluminum alloys. The precipitates prevent the movement of dislocations contributing to the strength of the metallic alloy. Geiger and Merklein[2] presented a study wherein a heat treatment with a duration of fewer than 1 s was sufficient to achieve softening effects. This data is important, in particular, for the realization of a localized heat treatment, which is essential for the successful implementation of the technology in its main applications. Aluminum has very high thermal conductivity, so localized heat treatment is a challenge[3]. In the vicinity of the laser focus zone, an area affected by heat also influences the flow of material during forming operations. The shorter the heat treatment duration, the smaller the thermally affected area will be.
Vollertsen and Hofmann[4] observed that, for several precipitation-hardening aluminum alloys of the 6000 series (AA6016, AA6181, AA6082) in the T4 state, it was possible to cause softening with short-term heating. The authors used a CO2 laser for heat treatment to improve sheet-forming capacity. On the other hand, the absorption of laser radiation by the aluminum surface is very low, so the sheet specimens were coated with a layer of graphite. Based on the very short heat treatment time, the effects associated with the heat-affected zone are limited so that the heat treatment can be located without the use of active cooling components. However, low absorption and strong contamination by graphite reduced the potential for industrial application. Optical diffracting elements are sometimes used to change the intensity of Gaussian distribution to a more top hat distribution, achieving a more homogeneous temperature on the laser beam focus area[5]. Geiger and co-authors[6] developed a different approach, achieving better absorption using an Nd: YAG laser, thus eliminating the need to use the graphite layer. The authors also demonstrated that the maximum temperature is the most important parameter that influences mechanical properties. Heating, maintenance, and cooling times are of secondary importance. In addition, the authors presented a thermomechanical simulation, which made it possible to simulate the heat treatment and subsequent forming operations. The simulation was then developed by Geiger et al.[7] with an inverse approach, allowing the calculation of appropriate laser heat treatment parameters. The consecutive cycle of heating and cooling introduced by a multi-path laser heat treatment strategy for a large-scale local laser heat treatment was investigated by Merklein et al.[8]. Laser beam energy has proven to be effective in homogenizing the temperature of large-scale areas. Expecting a sharp transition between treated and non-heat-treated zones to enhance the formability of THTB, self-quenching without any additional cooling was the most appropriate of the three tested methods. DSC thermal analysis is a powerful tool to identify precipitation/dissolution reactions of metastable phases[9]. Since higher heating rates shift dissolution reactions towards higher temperatures, Osten et al.[10] developed continuous heating dissolution diagrams for several aluminum alloys, which can be used to optimize heat treatment parameters. Hence, the selection of maximum temperature depends on the value of the heating rate. Frocker et al.[11] determined the optimal process window for AA6060-T4 local laser heat treatment based on the correlation between heating rate and peak temperature. Besides heat treatment parameters and their influence, the cold-forming process should be performed soon after local heat treatment. Natural aging (NA) was observed to play a key role, limiting the enhanced formability of tailored blanks[11-12]. Processes that occur during NA temporal evolution are to be first dominated by the movement of vacancies and silicon solutes, followed by the movement of magnesium[13]. In addition, the process window can also be narrowed due to the use of dry lubricant[14].
Dimensional accuracy should be assured to implement automated processing of THTB. For that, distortion during local heat treatment must be mitigated. Kahrimanidis et al.[15] developed an approach to minimize the distortion of 6xxx THTB using demonstrator parts. Their research has concluded that distortion is minimized by applying elastic deformation to the blank during the heating process.
Merklein and Vogt[16] developed heat treatment layouts for more complex geometries and validated the results with experimental implementation and forming of parts. The results were finally consolidated through universal guidelines for the design of components made of precipitated aluminum alloys using localized heat treatment. Merklein's research team and co-authors[17] also patented a new approach to produce aluminum sheets and components with stable mechanical properties, using a local quench after solubilization heat treatment.
Hogg[18] investigated the localized heat treatment of 5000 series aluminum alloys, having carried out a comprehensive analysis of different heating technologies. For the softening of the alloys, temperatures between 500 Celsius and 540 Celsius and waiting times longer than 30 s are necessary. Lattanzi and co-authors[19] conducted local laser heat treatment only in the central part of a unique dog-bone specimen of AA5754-H32. Their approach was found to be effective making both the material characterization less time consuming and material consumer. The association of each peak temperature with the corresponding stress-strain curve allows the local assignment of material properties along the aluminum sheet, whereby the accuracy of numerical analysis can be improved. The flexural test properties of the AA2012 aluminum alloy were investigated after local laser heat treatment by Mohammadi et al.[20], having found that the elastic return can be reduced by 43%.
Peixinho and co-authors[21] experimentally validated a localized heat treatment approach for application in the initiation of deformation zones of tubular structures for crashworthiness applications (triggers). It was possible to define a set of parameters using a laser source that proved to be effective in obtaining deformation modes with initiation in the area subjected to local softening. In this implementation, the approach was validated in tubular structures made of 6000 series aluminum alloy.
Piccininni et al.[12] studied laser heat treatment application on the deep drawing of an age-hardenable Aluminum alloy (AA6082-T6) using an experimental/numerical approach. Preliminary material characterization was aimed at investigating the material behavior in different conditions: as-received; in the supersaturated condition (obtained by physical simulation) and after being locally affected through laser heating. A Finite Element based approach was used to design the laser treatment of the blanks to be subsequently deep drawn at room temperature: a 2D axisymmetric model of the deep drawing process was coupled with an optimization routine in order to define the radial extent of the laser heat-treated area that can maximize the Limit Drawing Ratio. Experimental tests were conducted for validation purposes and revealed the effectiveness of the approach that enabled the improvement ofthe drawability by more than 20 % with respect to the as-received condition (T6). The drawability of an ultra-fine-grained sheet material AA6014 was improved since material flow moved from the softened towards crack-critical areas[22].
Tailoring material properties in multistage forming operations is also useful, as demonstrated by the research developed by Merklein et al.[23]. Applying an intermediate local laser heat treatment, the circular cup geometry part was produced without failure. That result is supported by the fact that softening of aluminum alloys is possible after pre-straining[24]. The effectiveness of combining the hydromechanical deep-drawing process with THTB was analyzed by Piccininni et al.[25].
Kahrimanidis et al.[26] demonstrated that local heat treatment enhanced the forming limits of more complex geometric parts, such as an automobile tailgate, even though the heating was carried out by conduction with a heating time of 3s. Machhammer et al.[27] by the use of the same heating tool studied the effect of both different peak temperatures and layouts.
The use of local heat treatment to improve the formability of aluminum alloys has the potential to enable further weight reduction in relevant structures. The scope and objectives of this work are intended to progress a step closer to industrial implementation, aiming for a Technology Readiness Level TRL4, based on the analysis of literature and further enhancing the understanding of the problem. The ability to use an industrial laser for the material heat treatment can contribute to such progression, as well as the testing protocol being performed in an alloy in industrial use by the project partner company (Bairrimoldes).
2. Materials and Methods
The analyzed alloy is a 6000 series aluminum (AA6063-T6) having a sheet thickness of 2 mm. Table 1 presents the chemical composition that was obtained in a spectrometer Phillips X´Unique II. Quasi-static mechanical properties were obtained following EN 10002-1 standard using a universal tensile testing machine (Instron, 25 kN). The tensile yield strength at 0.2 % offset (Rp0.2), Ultimate Tensile Strength (UTS), and elongation to fracture for an initial gauge length of 60 mm are presented in Table 2.
Table 1 Chemical Composition of the Tested Alloy (WT%)
Table 2 Mechanical Properties
As Differential Scanning Calorimetry (DSC) is a powerful tool to identify both precipitation and dissolution reactions, DSC thermal analysis was carried out in AA 6063-T6 in its initial state prior to any laser heat treatment. The sample was heated from room temperature up to 400 °C, the heating rate was small enough in order to make possible individualization of endothermic/exothermic peaks, assuming the value of 0,09 K/s in an Argon atmosphere (50 mL/min). Pure aluminum (99,99 %) was the reference material and the mass of the sample was 13 mg. DSC Q20 device was employed. Handling of data was performed so that dissolution/precipitation mechanisms could be identified and analyzed. Figure 1 depicts the specific heat capacity against temperature. This data is then used to determine peak temperatures for laser heat treatment strategy, in agreement with heating rate limits reached by laser equipment.
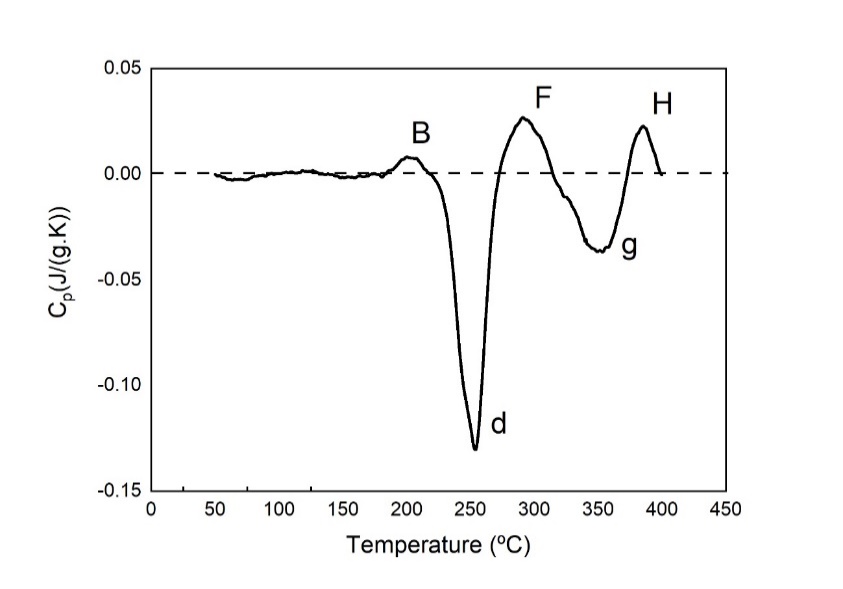
Fig. 1 Normalized DSC Specific Heat Capacity Curve of AA6063-T6 for a Heating Rate of 0.09 K/s
Laser heat treatment was performed using a Mergenthaler LM100 laser equipment that includes a pyrometer for non-contact temperature measurement used as the main information source for the laser power control algorithm. The selected focus region was a 10x10, 20x10, and 60x10 () area highlighted in the specimen design presented in Figure 2, depending on the strategy applied. With respect to strategy 1, the cylindrical laser beam has experienced no movement. On the other hand, strategies 2 and 3 had a constant linear speed of 1 mm/s. the laser beam diameter remained invariable, assuming the value of 10 mm for good temperature uniformity along specimen width. Figure 3 presents the laser equipment, specimen, and developed fixture for positioning.
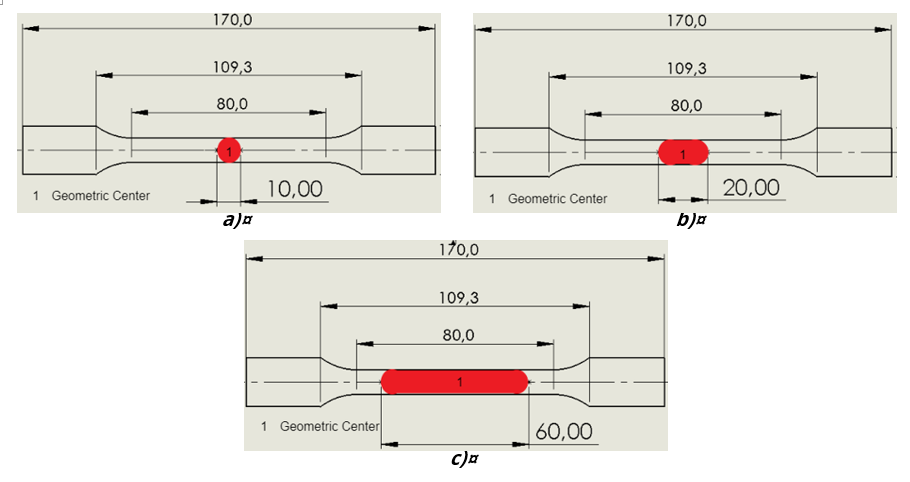
Fig. 2 Specimen Design and Laser Focus Area: a) Strategy 1 – 10x10 ; b) Strategy 2 – 20x10 ; c) Strategy 3 – 60x10
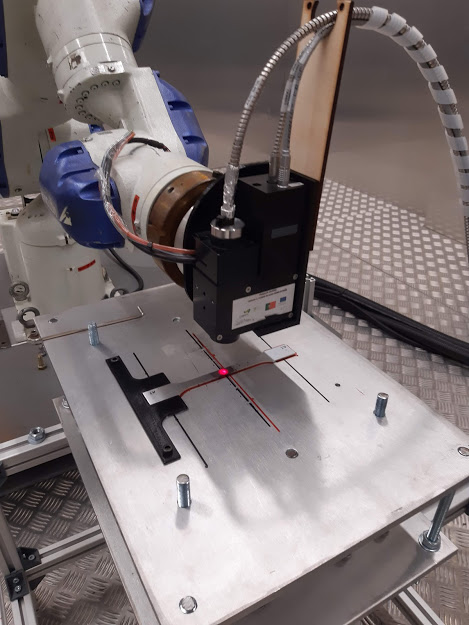
Fig. 3 Specimen Fixture and Laser Head
The experiment design included different target temperatures for the local laser heat treatment, with the objective of evaluating: if both specimen faces are to achieve a reduction in hardness; the evolution of hardness along a longitudinal axis with origin at the laser focus center; the natural aging phenomenon effect on hardness recovery; overall specimen behavior in a tensile test. Table 3 presents the test temperature for each specimen reference. The specimen reference “BM” refers to base material without heat treatment. Some of the target temperatures were not easily obtained due to difficulties with surface reflection, which is considered in the presented heating rate. The evolution of the heat cycle could be evaluated and graphically presented for each test, an example presented in Figure 4. As the temperature increases, the higher the losses due to radiation, air convection, and heat conduction, and, thus, the heating rate is not constant. A nominal heating rate corresponding to a linear approximation is presented in Table 3. Each heat-treated sample was coated with “GRAPHIT 33”, as such product intends to reduce the reflectivity of aluminum alloys.
Table 3 Specimen Reference and Test Temperatures
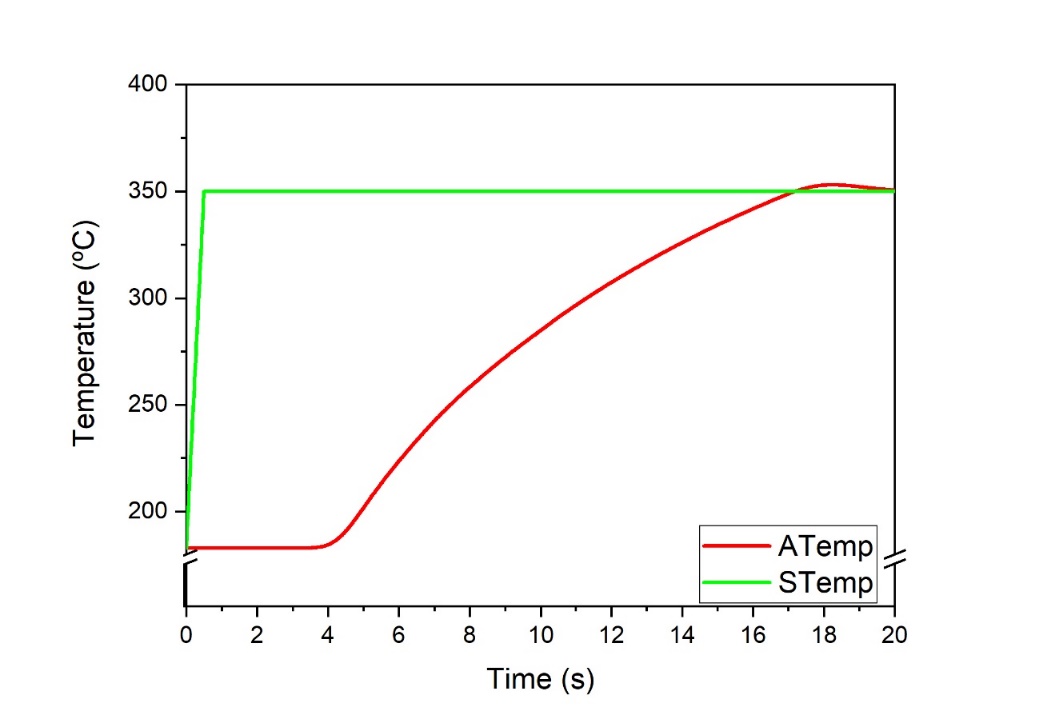
Fig. 4 Example of Heating Curve for Test Ref. A2
3. Results and Discussion
The values of Rp0.2, UTS, and elongation to fracture are presented in Table 4 as average results for the indicated test temperatures. Figure 5a) presents graphically the evolution of yield stress (Rp0.2), UTS, and hardness. Figure 8 presents representative stress-strain curves. For the sake of evaluating the effects of increasing the Heat Affected Zone (HAZ), Figure 9 displays the modified mechanical properties at a peak temperature of 400 °C. Tensile tests were performed 24h after local laser heat treatment.
Hardness was measured in different positions using a Vickers indenter on a Galileo D200 durometer. The measurement points include the laser focus zone in the incident surface and the opposite surface of the specimens. The heat-affected zone was analyzed by extending hardness measurement points along the longitudinal axis of the specimen. Results for the hardness measurements are presented in Figure 5b) for the different test temperatures. Figure 6 presents the hardness evolution along the specimen according to the HAZ of 10x10 , 20x10 and 60x10 , respectively. The specimen with the smallest heat-treated zone was the one that obtained the highest hardness reduction. Lastly, Figure 7 evaluates the natural aging effect on hardness measurements over time.
The analysis of hardness results enabled the identification of suitable heat treatment temperatures in the range of 365 to 450 °C that could provide a significant reduction in hardness. According to Figure 5b) it can be observed that the maximum hardness reduction of 32 % occurs at a selected maximum temperature of 400 °C. Instead, at 353 °C the hardness reduction is less pronounced.
Furthermore, this hardness reduction was observed for both the incident and opposite surfaces of the specimens, although the magnitude of reduction was slightly higher on the incident surface, as expected. The average hardness value for the HAZ of 60x10 at the incident and opposite surface assumes the value of 73 +/- 1.6 HV and 74.8 +/- 1.9 HV, respectively, showing that the temperature uniformity along HAZ is successfully achieved. Even so, measured hardness at the laser’s beam edge extension reveals a hardness increase. This can be sustained by the fact that the closer to the center of the laser beam, the higher the power intensity (Gaussian distribution).
Concerning hardness recovery due to natural aging from Figure 7, it can be concluded that the maximum temperature influences the microstructural evolution over time. For a maximum temperature of 365 °C and 455 °C, the hardness recovery is 6 and 19 %, respectively. The higher the heating temperature, the greater the number of MgSi clusters dissolved in the aluminum matrix and the greater its precipitation capacity at room temperature.
The main challenge for an effective modification of material behavior with the laser heat treatment for this particular alloy was concerned with radiation reflection. This could be mitigated by recurring to a graphite coating following several iterations.
Table 4 Specimen Reference and Mechanical Properties

Fig. 5 Variation of Mechanical Properties with Heat Treatment Temperature: a) Strength Properties (MPa); b) Hardness at Laser Focus Center at the Incident and Opposite Surface
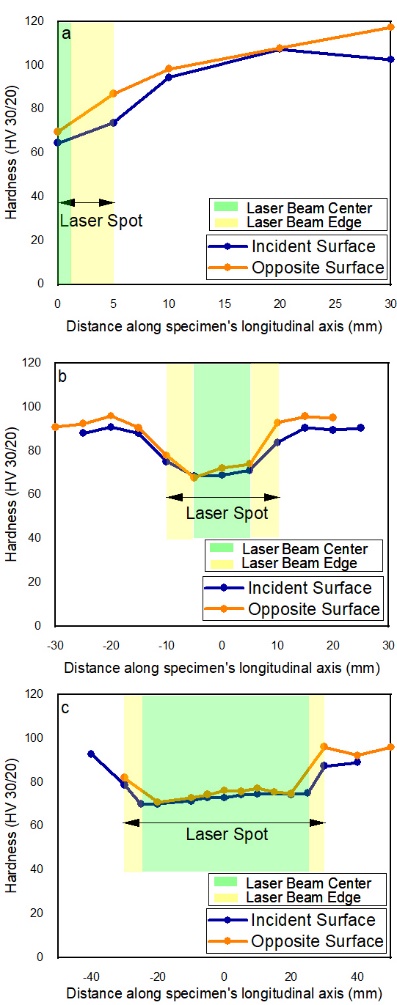
Fig. 6 Variation of Hardness along Specimen's Longitudinal Axis. Origin set at Specimen's Geometric Center: a) HAZ- ; b) HAZ- ; c) HAZ- ;
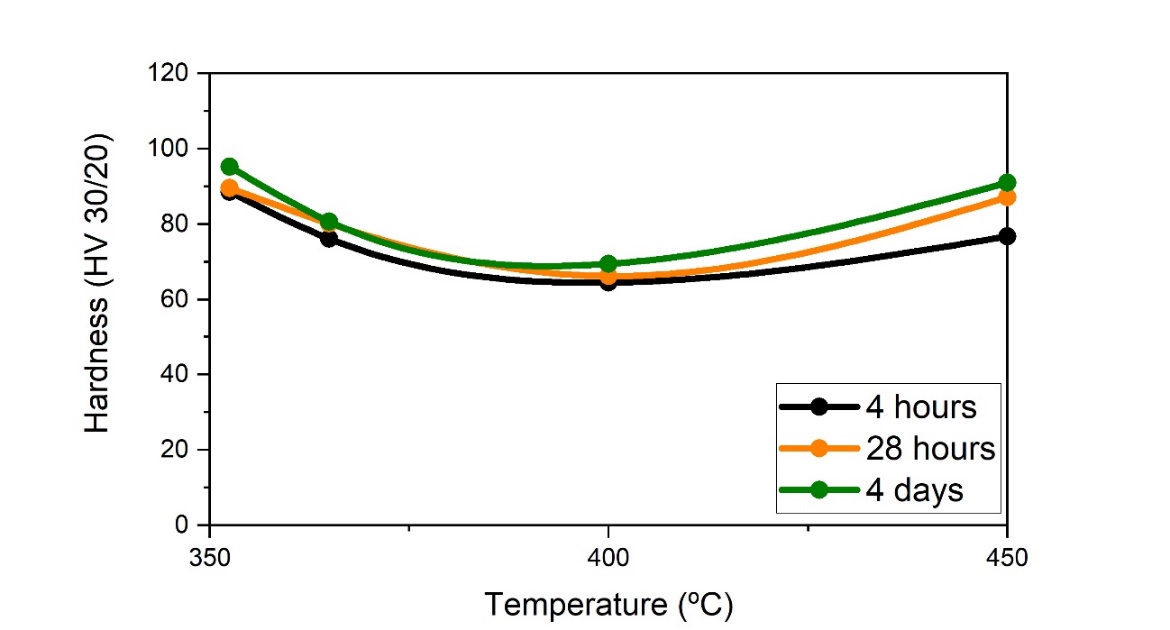
Fig. 7 Evolution of the Natural Aging Phenomena at Laser Beam Focus Center: from 4 Hours to 4 Days after Local Laser Heat Treatment
In order to allow for efficient local material modification, the stress-strain properties need to be analyzed with two objectives in mind: the validation of hardness results and choice of laser and processing parameters; obtaining material properties suitable for material modeling in finite element software simulations. Such numerical simulations can allow the definition of suitable areas for localized laser heat treatment that can provide effective improvements in forming representative parts. From the information provided in Table 4 and Figures 5, 8, and 9 it can be concluded that the heat treatment allows for a significant modification of material properties. In specific, the hardness results correlate well with the modification in mechanical properties obtained as a function of maximum temperature: a reduction in yield stress and Ultimate Tensile Strength is verified, in the range of 380 – 455 °C. The maximum softening is reached at 425 °C, corresponding to a Yield and Ultimate Tensile stress decrease of 34 and 31 %, respectively. Furthermore, similar to hardness results, the tensile test reveals no softening effect at a peak temperature of 353 °C. However, such modification is also observed in the elongation to fracture. This effect must be carefully considered although in typical laser-assisted forming applications, the area chosen for material modification is not located in critical forming zones[16].
In view of the drastic decrease in the elongation to fracture, results depicted in Figure 9 suggest that an increase in the HAZ enables recovery of the ductility at a peak temperature of 400 °C, sustaining that a greater number of MgSi particles are dissolved in the aluminum matrix. At the same time, a small variation in mechanical resistance is observed: Yield and Ultimate Tensile Stress assume the value of 164,5 +/- 7 e 189,0 +/- 8 MPa, respectively.
Another important factor to consider for effective industrial implementation of this approach is that the heat-affected zone must be sufficiently small in order not to affect the overall mechanical behavior of the part or negatively influence forming behavior through a generalized reduction in elongation to fracture. The results presented in Figure 6 suggest that, for the most relevant temperature and test condition, the heat-affected zone extends circa 5 mm from the last point of the center laser focus track. The sharpest this transition between affected and not heat-treated material, the higher the potential for increased formability in blanks’ application. In order to do so, this length can be reduced with higher heating rates, which is regarded as a future research direction.
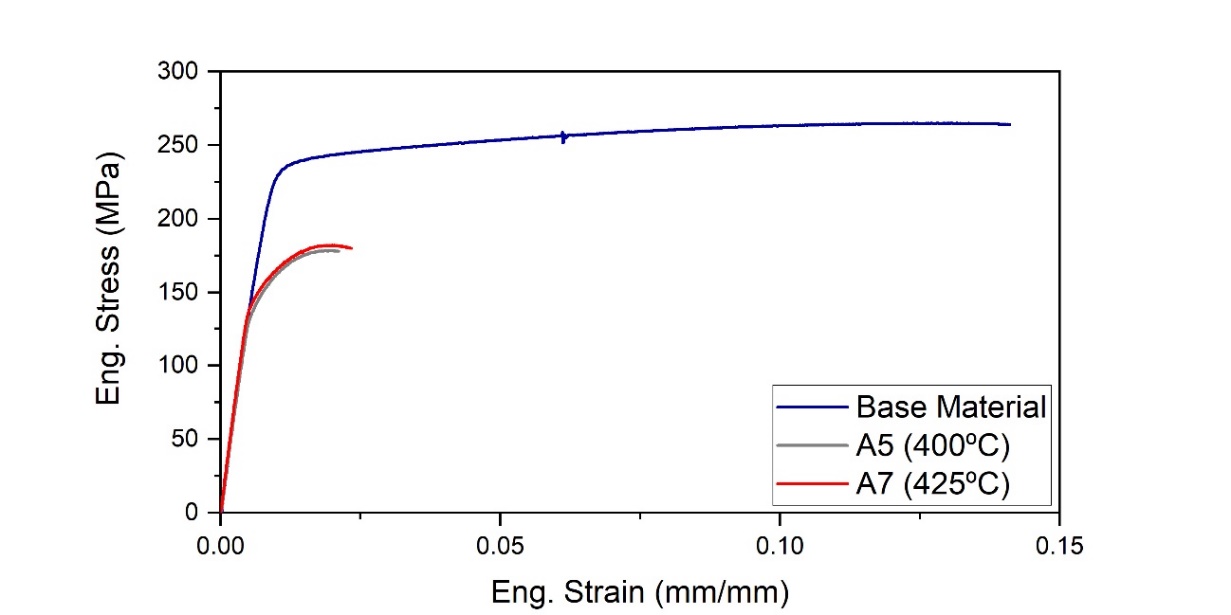
Fig. 8 Representative Stress Strain Curves
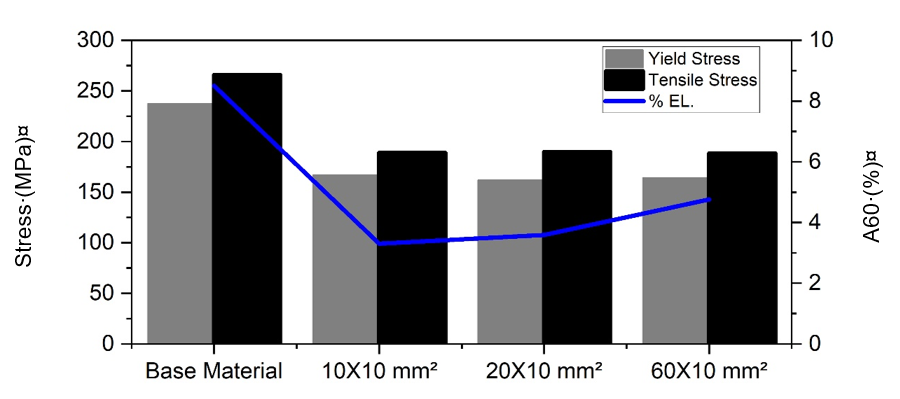
Fig. 9 Evolution of Mechanical Properties according to the increased Heat Affected Zone (HAZ) for a Maximum Temperature of 400 °C
4. Conclusions
This study presented information regarding the development of a localized laser-induced heat treatment for 6063-T6 aluminum alloy. Such a process is intended to improve the forming behavior of aluminum parts in challenging metal-forming conditions. A laser heat treatment method and relevant parameters and a testing procedure on 2 mm thickness specimens suitable for tensile testing were described. Based on the literature review the temperature is considered the most relevant parameter, which was validated in this study.
It was concluded that it is possible to locally modify yield strength and hardness using laser control parameters. A suitable test temperature range was identified. A positive effect of material softening was observed in both hardness and strength properties. The natural aging phenomenon plays a key role in industrial applications, and therefore, the component must be processed right after the localized heat treatment, so that the recovery of the sheet's mechanical strength does not compromise the plastic deformation process. Concerning the reduction of ductility, as the HAZ increases, the elongation of fracture is closer to its initial values, without any significant influence on the mechanical resistance. With that in mind, it is recommended that for the correct material characterization purposes the local laser heat treatment should be executed to the entire blank, after which the specimen should be cut. The dimension of the heat-affected zone should also be considered in the design of the industrial implementation and associated numerical simulation tools. It is considered feasible that different heating rates can be beneficial for application in commercial use.