INTRODUCTION
In recent years, agricultural sector has faced many challenges like urbanisation, climate change, resource limitation, food waste, but the major challenge it faces is meeting the food needs of a rapidly growing number of people. United Nations predict that there will be 9,6 billion people in the world in 20501. In order to provide food for the entire population it is important to merge modern information and communication technologies with agriculture to perform intelligent farming2 and improve productivity. IoT is a technology that has great potential in this aspect and offers innovative solutions for agricultural sector modernisation. The Internet of Things (IoT) was first mentioned in 1999 when MIT’s Kevin Ashton stated that “adding RFIDs to everyday objects would create an Internet of Things”3,4. The most comprehensive definition of IoT is given by IEEE IoT initiative5 in their document with baseline definitions of IoT. They separate definitions for small systems which contain uniquely identifiable things and small sensors, and complex systems that interconnect millions of things with a capacity to deliver complex services. IoT for low complexity systems is defined as5 “a network that connects uniquely identifiable ‘things’ to the Internet. The ‘things’ have sensing/actuation and potential programmability capabilities. Through the exploitation of unique identification and sensing, information about the ‘thing’ can be collected and the state of the ‘thing’ can be changed from anywhere, anytime, by anything”. IoT for complex systems is defined as5 “a self-configuring, adaptive, complex network that interconnects ‘things’ to the Internet through the use of standard communication protocols. The interconnected things have physical or virtual representation in the digital world, sensing/actuation capability, a programmability feature and are uniquely identifiable. The representation contains information including the thing’s identity, status, location or any other business, social or privately relevant information. The things offer services, with or without human intervention, through the exploitation of unique identification, data capture and communication, and actuation capability. The service is exploited through the use of intelligent interfaces and is made available anywhere, anytime, and for anything taking security into consideration”. In other words, IoT focuses on process automation as to lessen human interaction. During the automation process IoT uses sensors to collect data, processes the collected data using controllers and actuators are used to complete the automation process6. There are numerous application areas of IoT, which include, but are not limited to: smart cities, smart agriculture, smart power grids, smart health, smart transport, smart buildings, smart living solutions, smart human settlements and other7. In recent years, IoT applications have increased, especially in smart cities, smart homes, smart agriculture and smart healthcare8. IoT offers multiple benefits in before mentioned areas through innovative technologies and solutions. Application of IoT in agriculture allows monitoring and control of the entire process by using different sensing, mobile, big data and other technologies. IoT offers numerous benefits for agriculture such as optimisation, control and automation of processes which were previously done manually9. IoT monitoring systems in agriculture improve the food quality but also productivity and safety aspects10. Farooq et al.11 identified three main application areas of IoT in agriculture: precision farming, livestock and greenhouses. Each of these areas has different fields, one of which is seed germination and seedling development. This is arguably one of the most important phases and as such is the focus of this article. In order for germination to happen, seeds need to have the proper amount of moisture, oxygen, light and temperature12. The area in which seed germination and growth occurs under controlled and monitored conditions is called a grow room. Harun et al.13 identify IoT, specifically IoT-based monitoring systems as a means to achieving a higher percentage of germination and seedling growth. The aim of the article is to propose a novel IoT-based self-sustaining micro grow room architecture for enabling and optimising the seed germination and seedling development pro- cess. One of the main goals is to develop a system that can be deployed efficiently, with minimal financial costs and energy footprint, which would enable its practical usage primarily in private self-sustainable households. The architecture proposed within this article offers remote control, data processing and visualisation, data trend tracking, smart optimisation, actuator control and event notifications. The aim of the article will be accomplished through four sections. This section gives an introduction to the topic of IoT in general and its application and importance in the field of agriculture, while section 2 focuses on existing solutions and state of the art research on the topic. Through section 3 detailed description of the proposed IoT-based grow room architecture and its components is given. In the end, the experiments are conducted, the results discussed and advantages of the proposed system are described.
RELATED WORK
As mentioned earlier, there are three main application areas of IoT in agriculture: precision farming, livestock and greenhouses11. The focus of this article is seed germination and seedling development so this literature review will focus on application of IoT in greenhouses, with emphasis on IoT in grow rooms. While conducting the literature review, research string was defined ((“Internet of Things” OR “IoT”) AND (“grow room” OR “plant nursery” OR “greenhouse”)) and databases for research were defined (IEEE, Elsevier and Web of Science). After the search was conducted, only articles in the last five years were selected which left 42 articles. All of the articles were not relevant and after title, keywords and abstract screening, fifteen most relevant articles were selected for further review. Out of the fifteen articles, seven of them focused specifically on IoT in grow rooms9,12,14-17. The overview of the selected articles can be seen in Table I. The article by Kodali et al.19 describes a model of a smart greenhouse where different actions are carried out according to information collected from different sensors. Irrigation is carried out according to the soil moisture threshold so that optimal amount of water is applied to the plants. From soil health card data, proper amount of nitrogen, phosphorus, potassium and other minerals can be applied by using drip fertigation techniques. Water management tanks are filled with water after measuring the current water level using an ultrasonic sensor. Growing lights are used to provide plants with the requisite wavelength light during the night. Humidity and temperature sensors regulate the humidity and temperature of the greenhouse by using a fogger. Bee-hive boxes are deployed for pollination and boxes are monitored using ultrasonic sensors to measure honey and send mails to the buyers when they are filled. The authors implemented the proposed model, but the research does not show the differences between plants in a smart greenhouse and those in a regular greenhouse. Li et al.20 propose a smart system of greenhouse management based on the IoT using sensor networks and web-based technologies. The sensor network consists of the master control center and various sensors using Zigbee protocols and the proposed system consists of six functional modules: user management module, hardware node management module, system control module, network settings module, monitor module and weather module. The article by Pallavi et al.21 proposed a remote sensing of agriculture parameters and control system to the greenhouse agriculture. The system is designed to remotely monitor the greenhouse parameters such as CO2, soil moisture, temperature, and light. The system also controls different actions like greenhouse windows/doors roll on/off based on the soil moisture levels. The results are analysed for different greenhouse parameters such as CO2, soil moisture, temperature, and light for bell pepper plant. The drawback of this article is that there is no comparison between the results of regular greenhouse and the one proposed in this article. Biqing et al.22 designed a sugarcane growth monitoring system to realize real-time monitoring of sugarcane growth and analysis of collected data. Collected data include temperature and humidity, sunshine, CO2 and plant height. Users logged in the system can effectively monitor growing environment of sugarcane and implement remote visual management and improve their production efficiency. The drawback of the pro- posed monitoring system is lack of automation and controlling possibilities. The authors Yang et al.8 designed and implemented an indoor intelligent agricultural IoT system that adopts a three- layer framework: data sensing layer, cloud service layer and user interaction layer. The solution is described in detail, from hardware, systematic service to application. The system monitors temperature, humidity, illumination intensity and content of CO2, O2 and NO2 in the air. Based on analysis results, guidance of plant cultivation is given to user. The objective of the research by Islam et al.12 research was to develop an IoT Smart Germination Assistant system to improve the seed germination process. Multiple sensors are used to measure, adjust and control the moisture, humidity, pH level, temperature, and sunlight to the standard value for each crop. The proposed system was implemented and tested with 300 seeds of jute leaf. The experiment showed that the developed system is more effective and efficient than the natural system of seed germination. As only one evaluation experiment was conducted on one type of crop, definite conclusions cannot be drawn as results may vary depending on the seed type, location and environment. Gonzalez-Amarillo et al.23 present the design of the IoT-based greenhouse model for the tracking and record keeping of seedlings in the germination and growth stages. The model tracks luminosity, humidity, temperature, and water consumption to reveal overall water use, growth patterns of the plants, and the timeline for harvest of produce. The system also allows automated control of the greenhouse environment using an irrigation system or temperature control and presents traceability of agricultural products from seed to final produce. The proposed system reduces water and energy consumption in the process. In the article14 Somov et al. demonstrated the application of IoT in agriculture, more specifically, in tomato greenhouse. Based on the data from different sensors (pH, electric conductivity, solution flow, temperature, photosinthetically active radiation, humidity, CO2) the growers can make better decisions on a number of issues, predict the crop growth rate, time tomato harvesting and ensure control of the greenhouse conditions based on mentioned data.
Reference | Source | Year | Location | Application |
Protocol/ Network | Sensors | Crop |
19 | Conference | 2016 | Greenhouse | Monitoring | WiFi | Ultrasonic, moisture, temperature and humidity, LDR | N/O |
20 | Conference | 2017 | Greenhouse | Monitoring | Zigbee | Temperature and humidity | N/O |
21 | Conference | 2017 | Greenhouse | Controlling | WiFi | CO2, soil moisture, temperature, light | Bell pepper |
22 | Journal | 2018 | Greenhouse | Monitoring | ZigBee | Temperature, humidity, sunshine, CO2 | Sugarcane |
8 | Journal | 2018 | Greenhouse | Monitoring |
4G, WiFi | Temperature, humidity, illumination intensity, CO2, O2, NO2 | N/O |
12 | Conference | 2018 | Grow room | Controlling | GSM | Moisture, humidity, pH level, temperature, sunlight | Jute leaf |
23 | Journal | 2018 | Greenhouse | Controlling | WiFi | Soil humidity, air humidity, temperature, luminosity | N/O |
14 | Journal | 2018 |
Greenhouse and Grow room | Controlling | WSN | PH, electric conductivity, solution flow, temperature, photo-sinthetically active radiation, humidity, CO2 | Tomato |
24 | Conference | 2018 | Greenhouse | Controlling | N/O | Electrical conductivity, pH, water temperature, air temperature, humidity | N/O |
9 | Conference | 2019 | Grow room | Controlling | WiFi | Temperature, humidity, luminosity, soil moisture | N/O |
15 | Conference | 2019 | Grow room | Controlling | WiFi | Soil moisture | Cocoa |
16 | Journal | 2020 | Grow room | Controlling | WiFi | Soil moisture | N/O |
17 | Conference | 2020 | Grow room | Controlling | WiFi | Temperature and humidity, current, soil moisture | N/O |
18 | Journal | 2020 | Grow room | Monitoring | WiFi | Temperature, humidity |
Ocimum basilicum |
25 | Conference | 2020 | Greenhouse | Monitoring | WiFi | Resistive soil moisture, Capacitive soil moisture, temperature, humidity, light | Spinacia Oleracea and Lactuca Sativa |
The authors also applied Reinforcement learning to find optimal light usage. Palande et al.24 focused their research on hydroponic greenhouse. They created a system that can grow plants and vegetables and can operate without depending on the outside climate. They used hydroponics, a method of growing plants without using soil. They automated the system by using microcontrollers and sensors (electrical conductivity probe, pH sensor, water temperature sensor, air temperature and humidity sensor) to reduce human intervention. The proposed system is fully automated, but also small and affordable enough for consumer usage. Cruz et al.9 describe the architecture of a mini-greenhouse monitored via IoT. Sensors are used for monitoring and control of the variables that most influence the plant development (temperature, humidity, luminosity and soil moisture). The proposed system consists of a cloud-based storage, web platform, controllers and sensors. The prototype was developed but no experiments were presented. The major advantage of this system is that it uses open source software and generic hardware so the system allows adding new sensors. Unlike previously mentioned research, articles by Jaafar et al.15 and Methsarani et al.16 focus only on irrigation control. Jaafar et al.15 designed an automatic drip irrigation system based on IoT platform which shows better results in plant height and number of leaves than traditional systems. Methsarani et al.16 developed a wireless smart irrigation system which helps in saving money and water. The system checks the soil moisture level and the water need of the plant and can be used to switch on/off the watering valve. Phirke et al.17 designed a Smart Plant Incubator prototype to simulate the optimum atmospheric conditions like temperature, soil moisture, air humidity and light intensity required for the best growth of a specific plant. The incubator is fully automated and plant growth efficiency is maximised. The prototype provides automation and no human is required to monitor changes as it automatically uses the stored data and simulates the climatic conditions. The article by Franco et al.18 presents a monitoring system for the germination of Ocimum basilicum seeds. The system controls the temperature and humidity variables through the strategy of fuzzy control. Also, it uses image processing for seed monitoring. The germination tests carried out under controlled factors, show results with positive growth trends compared to the tests run under uncontrolled factors and on timed hydration regime. The application of a constant temperature and maintaining a high level of humidity inside the germination chamber, it results in obtaining a short hydration period and obtaining radicle with elongation between 3 to 10 mm. Similarly, monitoring the seeds without interrupting the temperature and humidity level by opening the germination chamber reduces a positive result to the decrease of non-germinated seeds. Marcos and Mai25 present a system that helps assist indoor plant growers using IoT. The purpose of the article is mainly focused on determining which light is more suitable for growing Spinach (Spinacia Oleracea) and Lettuce (Lactuca sativa), but the authors also implement an automated greenhouse system using IoT to determine the feasibility of having an intelligent monitoring system for indoor plant growth. The purpose of the implemented system is to determine the effects of different plant grow light spectra/colours in terms of temperature, humidity, light intensity, and soil moisture. From the conducted literature review, we can see that there are not many articles on application of IoT in grow rooms or plant nurseries. Most of the research focuses on greenhouses in general8,19-25, but grow rooms, as much as they are similar to greenhouses, also have specific requirements. If the articles are analysed according to used
sensors, Figure 2 shows that the most often used sensors are temperature sensor, followed by humidity, soil moisture and light sensor. On the other hand, if the articles are classified by protocol/network used, Figure 1 shows that WiFi is most commonly used and Zigbee, GSM and WSN are rarely used in state of the art research. The most prominent demerit of the surveyed articles is that most of the articles suggest different systems and prototypes, but only a few12,18,24, show experimental results of the proposed systems and compare the results with the results from regular greenhouses or grow rooms. Also, many of the articles analysed8,18-20,22,25 focus only on monitoring different variables and not on automation of agricultural processes.A PROPOSED IOT-BASED GROW ROOM ARCHITECTURE
The proposed architecture describes a self-sustaining IoT-based system which aims to optimise seed germination and seedling development parameters in a controlled micro-climate environment. The system is modular and scalable from two perspectives; (1) its functionalities (and consequently its complexity) can be scaled up and down according to individual requirements by adding or removing modules, without the need for re-configuring the architecture or reprogramming the main code, and (2) a grow/host room can contain one or more smaller-scale grow rooms, each of them controlling their own environment independently. The former can be argued by the user’s needs and environmental conditions (for example, there might not be a need for a heater unit if the grow room receives adequate ambient temperature, or a need for camera if the user does not require advanced AI capabilities. The latter can be argued by the heterogeneous needs of each different plant types, where each of them require their own optimised micro climate and conditions. Because of these requirements, it is essential that the system implementation has reasonable costs and effectiveness. In one of the most basic forms, the system might consist of a temperature sensor, an MCU, a heater element and grow lights. The temperature sensor reads the air temperature, sends it to the MCU unit, which processes the data, regulates the actuators and sends the data to the cloud and to user endpoints. If the MCU detects low threshold temperature or trend for example, it activates the heater element and sends the event notification and parameter data to the cloud and to user’s phone application and/or email. This is a simple automation example coupled with an IoT networking, actuator control, data processing and cloud visualising capabilities. More advanced grow room modules involve humidity tracking (both air and soil humidity) and regulating ventilation and irrigation subsystems; measuring luminosity values and regulating grow lights; applying machine learning methods in detecting and recognising plant development phases and fine-tuning grow lights’ parameters such as wavelengths and intensities accordingly. Thus besides a simple automation, the architecture offers remote control and data processing and visualisation, data trend tracking, smart optimisation and actuator control, etc. The AI module could act proactively by analysing data trends (for example, continuous drop in temperature values, and/or weather forecast via third-party API) and act on the actuators in a way to prevent temperature, moisture and/or luminosity shocks to the seedlings. The system’s parameters could be customised for individual plant type, as not all plants require the same amounts or intensities of light, moisture, air temperature, etc.
The Figure 3 presents the proposed architecture’s main building blocks, general connectivity options and cloud interfaces and functionalities. As illustrated, the Edge part of the architecture (physical location of the seedlings called The Host Room) can consist of one or more mutually independent micro grow rooms, all connected to the WiFi or mobile networking interface. Cloud services are represented in two categories: (1) monitoring – receiving real-time data, parsing and visualizing data via graphical interfaces and charts, monitoring data trends from location and from the third-party weather forecast service APIs, with the latter not implemented in the current version of the system and reserved for future research; (2) automation – logging data and creating data sets for future references, customised email and push notifications to user(s) in order to alert the user on critical events; artificial intelligence/machine learning module which could make decisions based on more complex set of input data (weather forecast, real-time trends, historical recorded data, etc.). The AI module was not implemented in the current version of the system and is also reserved for future research, where it will probably be implemented in the cloud environment because of the computational limitations of the ESP MCUs. Outside of the monitoring and automation categories there is a remote “manual” override which user can use in the event of technical failures (sensor and/or relay failures for example). The user can thus use the switch to directly control the heating, light, irrigation and other components outside the scope of automation and AI.BASIC SYSTEM IMPLEMENTATION
For the implementation of the proposed architecture, the following components were used: • housing: IP protected, weatherproof housing for the MCU and the electrical components, • microcontroller: ESP8266 SoC microcontroller, • code: C-based code for communicating with sensors actuators, reading values, parsing data, communicating with cloud services, etc., • small scale heating element (500W), • heating mat (17.5W) for aiding seed germination, • cloud API, • grow flood lights, • sensor array: Sensors for reading target parameters and sending data to the MCU, • network Gateway: WiFi 802.11 access point and Internet Gateway (alternatively, 3G/4G router), • ESP camera, • solder board with needed electronic components, • cloud services for monitoring, displaying and managing data and actuators, • web based task automator (an event triggering service); for example, for logging detected values onto online spreadsheets, Figure 4 illustrates grow room components in more detail. ESP Micro-controller is the core edge computing device with embedded WiFi capabilities, connected to the PCB and electronics, to power (AC or battery, or both), to sensors and to the actuators. Because some of the actuators are requiring more than 3.6V provided by the ESP8266 (heaters, lights, pumps, etc.), they are controlled via relays and are requiring connections to their own power sources. Sensor array is scalable, and might be composed of a subset of sensors for reading the following parameters: ambient temperature, ambient humidity, soil humidity, luminosity, 2D imaging, pH, air flow, pressure, and others. Actuators that could be used within the architecture are electrical heaters (up to 220V 16A with the current relay), water pumps, flood lights, fans, blinds motors, etc. The core of the grow room is seedbed itself. For small-scale applications, the grow room can be as small as about 0.5m3, hosting and managing for example about 200-300 pepper and/or tomato seedlings in their early development. Figure 5 shows the user cloud interface with numerical and graphical representations of recorded temperature and humidity fluctuation within the grow room throughout the chosen time period. The source code implementing the core of the IoT Grow Room system is publicly available on the GitHub service (https://github.com/tomicic/GrowRoom).
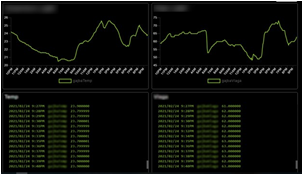
The experiments were conducted in northern hemisphere, continental climate, in February and March, when morning outdoor temperatures were recorded up to -7°C, and daily up to 16°C. One room of approximately 6m2 in size and 15m3 in volume was used as a host for 3 independent grow rooms, each in volume of about 0.5m3, managing the growth of bell pepper and various varieties of tomato seedlings. One batch of each tomato and bell peppers seedbeds were positioned outside the grow rooms, as sort of the control group, depending only on the shared electrical room heater and daylight. The used room heater was convectional, set to power on to 1kW convectional heating when room temperature drops below 10°C. Figure 6 roughly illustrates the positioning within the host room; heater was placed in the center of the room (drawn in grey); micro grow rooms (green) and un-managed seedbeds (red) were placed on the wall shelves. The proposed grow room system has prevented low temperature shocks to seedlings at numerous occasions, dozens of times per night and morning, at the period of two weeks, while ambient temperatures dropped well below the statistical average of that period of year at the measured location. In contrast, seedlings that were not protected by this architecture and were placed within a room with thermostat-based electrical heaters died off in significant numbers (about 20 %) or their growth was significantly impeded compared to the seedlings managed by the smart grow room. Small-scale heaters used within the grow rooms managed the temperature dynamics less abruptly combined with the heating effect of flood lights that were turned on in low light conditions, which also meant lower temperature conditions. True leaves were replacing cotyledons in much faster pace within managed grow rooms compared to un-managed seedbeds, which also showed irregular and inconsistent development dynamics (Figure 7).
Smart grow rooms provided additional LED illumination when there were low ambient light levels detected. Humidity sensors alerted the user when there was a need for watering the seedlings to optimal levels, and water pumps and other components of the small-scale irrigation system might fully automate this process within the architecture. All of the grow room parameters could be tracked in real time on cloud service, which was notifying users on critical events, temperature and humidity fluctuations, parameter trends and power consumption. The experiment ended at the moment the seedlings were ready to be transplanted to the field. The visual results clearly indicated that seedlings grown within managed grow rooms developed significantly stronger stems, more leaves and larger root system compared to the ones developing in manually managed seedbeds. The results are easily replicable by using the proposed architecture with described components.DISCUSSION AND CONCLUSION
In this article we have proposed a novel, IoT-based self-sustaining micro grow room architecture for the optimisation and management of seed germination and seedling development process. As detailed in Section III, more than one micro grow room can be located within the same physical location called the host room, and each micro grow room can have its own micro-climate and customised management enabled by the IoT and AI technologies. Compared to the existing solutions, the main advantages of the proposed architecture are as follows: (1) it is an affordable solution for home owners with easily obtainable components and non-complex implementation; (2) considerable energy savings because of the architecture’s modular and scalable design; (3) autonomous optimisation of micro-environments for seedling development. The first advantage can be argued by the usage of easily obtainable, inexpensive components, the plug&play design where the user should only connect the needed sensors and actuators, and with code that will be publicly available on the GitHub platform. The second advantage can be argued by the potential of the platform to be scaled according to the seedling’s number and/or seedbed sizes. In the presented experiment, the host room had a volume of 15 m3, while the micro grow room within was only 0.5m3 in volume and was able to host about 250 bell pepper and various varieties of tomato seedlings. Such a size optimisation itself results in a considerable energy savings in various heating modes. The same applies for the soil humidity levels, retaining humidity longer in such semi-isolated micro environments. The third advantage can be argued by the use of the IoT and AI technologies. Sensors, micro controller, cloud services and actuators can work autonomously in order to manage the development process. The use of AI could elevate the seedlings’ development optimisation to a more customised approach to each individual plant type and the development phase. Thus said, the implementation presented within this article did not include more advanced features of the proposed architecture such as the machine learning subsystem for plant development phase identification and related parameter customisation, which is reserved for the next phase of the research.