1. INTRODUCTION / Uvod
Currently, maritime transportation accounts for approximately 90% of the total volume of trade transactions [1]. It has the greatest economic benefit, energy efficiency, and safety [2-4]. It is known that sea vessels consume less fuel per ton of mileage compared to other types of transport [5]. Lately, maritime trade is continuing to expand worldwide, ahead of the expansion of other industries [6], which entails a concomitant process - an increase in greenhouse gas emissions, which poses a danger to the environment [4]. Currently, the shipping sector accounts for about 3% of total greenhouse gas emissions and 9% of transport-related emissions [7].
Negative emissions from ships that pollute the air include carbon dioxide, sulfuric and nitrogen oxides, volatile organic compounds, and solid particles [8]. In addition, negative emissions, interacting with atmospheric components, form additional harmful substances, such as aerosol particles containing sulfates, nitrates, and various organic substances [9,10].
For shipping to not lose its enormous potential and development dynamics, taking into account the fact that the demand for sea transportation is growing faster than the improvement of the consumer properties of motor fuels, it is necessary to update measures for the implementation of technological and energy transitions to reduce the level of environmental pollution. Applying green technologies and implementing decarbonization processes confidently come to the forefront of scientific research on marine topics. Decarbonization positively affects environmental health and plays a crucial part in the sustainable development of shipping [11].
Recently, the International Maritime Organization (IMO) revised the strategy for shipping decarbonization [12]. The new IMO strategy envisages achieving zero greenhouse gas emissions from international maritime transport by approximately 2050, with intermediate benchmarks of 20-30% by 2030 and 70-80% by 2040 [13].
Currently, diesel bunker fuel is traditional for ships [14]. The use of this type of fuel by shipping companies is due to its main positive characteristics-high thermal efficiency and low price, which allow ships to cover fairly long distances. Unfortunately, the use of fuel oil leads to the formation of high values of emissions of sulfur oxides, solid particles, and nitrous oxide [15]. These harmful emissions create problems for human health and pollute the environment.
Even under the new rules established by the IMO organization, according to which the sulfur content in marine fuel is reduced from 3.5% to 0.5%, harmful emissions will remain quite high [16].
In addition, the geographic expansion of emission control zones, where emission limits are even more stringent, requires the use of marine motor fuels with the lowest sulfur content. The cost of such fuel is much higher than conventional fuel [14].
One of the main ways of implementing decarbonization is the use of alternative fuels. Therefore, the search for environmentally safe alternative types of fuel is currently relevant for limiting the number of emissions of harmful substances into the atmosphere [17].
2. METHANOL AS AN ALTERNATIVE FUEL FOR SHIPS / Metanol kao alternativno gorivo za brodove
The main alternative types of marine fuel are biofuel, liquefied natural gas (LNG), ammonia, hydrogen, and methanol [18]. Technologies for the production of alternative fuels are currently developing at a fairly fast pace [4,19,20]. At the same time, when used in shipping, each of these types of fuel has its advantages and disadvantages.
The advantages of methanol compared to the main alternative fuels are that it is in a liquid state, as well as the possibility of a minor conversion of the existing infrastructure for engines and ships with the help of effective modernization [21,22].
Methanol (methyl alcohol) has the formula CH3OH. This is the simplest of the alcohols. Methanol is a clear, colorless liquid that ignites even at room temperature. Methanol was first obtained by the researcher Boyle in 1661 while studying the processes of wood distillation, and chemists Peligo and Dumas in 1834 established its chemical composition [23]. Later, various industrial technologies for obtaining methanol appeared [24]. The largest amount of methanol is used in the chemical industry. Industrial methanol is typically 99.85% pure by weight, according to the standard for methanol. The high ratio of hydrogen to carbon, characteristic of methanol, allows it to significantly reduce harmful CO2 emissions compared to traditional fuels.
For the safe use of methanol as a motor fuel for ships, the requirements of the IMO IGF safety code must be met. This document contains regulatory requirements for the safe operation of engines and all fuel infrastructure that operate on methanol. At the same time, the fuel infrastructure of ships is designed and manufactured so that crew members do not have direct contact with methanol [25].
Methanol can biodegrade and has a lower impact on the environment in the event of a spill [26]. When methanol enters seawater, it dissipates rapidly due to its high solubility and inability to bioaccumulate. The low risk of environmental damage from possible spills allows methanol to be stored at sea. According to the indicator of toxicity for the environment, methanol is safer than other types of fuels [25].
Methanol does not content sulfur and carbon-carbon bonds, so it does not form sulfur oxides, and as a fuel, it allows reducing emissions of solid particles during combustion. In addition, due to the lower adiabatic temperature of the flame, the release of nitrogen oxides (NOx) can be reduced [27]. The authors [28] found that when using methanol, NOx emissions per unit of energy are 45% lower than when marine engines run on traditional fuel. Similarly, adding water to methanol can control NOx combustion, resulting in the engine being able to meet Tier III NOx standards by eliminating EGR or SCR requirements [29]. The number of emissions of harmful substances during the combustion of methanol depends on the raw materials and energy carriers used during production [30].
Methanol, due to its liquid state in atmospheric conditions, has almost four times greater volume energy density than hydrogen [31]. In addition, compared to hydrogen and ammonia, methanol requires smaller storage facilities and less bunkering during long voyages [22].
A significant advantage of methanol over liquefied gas is that it does not require low temperatures and thermal insulation for its storage, so the designs of tanks and fuel tanks are very simple, and their cost is relatively low. Similarly, it is much easier to convert ship fuel tanks from conventional oil to liquid methanol than to install LNG tanks [21].
Methanol is an environmentally friendly fuel available in most ports and is much easier and more economical to store on board than gas. Due to its long history of safe handling, methanol is considered the least risky fuel compared to LNG, hydrogen, and ammonia [32].
This makes methanol a popular and viable alternative marine fuel that can help the marine industry gradually limit emissions, meet defossilation targets, and provide the expertise needed to develop more stringent marine fuel standards. It is attracting increasing interest from owners of ocean liners, coasters, ferries, cruise liners, and inland waterway vessels.
It is worth noting that methanol has been sold and transported in chemical tankers for many years. There is also the experience of offshore supply vessels and platform supply vessels that carry methanol for the marine industry, which can serve as a guide for the wider use of methanol as a bunker fuel. Methanol is a widely available, distributed commodity with a global distribution network that can easily be used to support marine fuel bunkering [33].
From a technical point of view, methanol can be adapted for use on ships on a large scale and is five to six years ahead of alternative marine fuels, including ammonia [25].
Based on research [34], the authors conclude that by 2050, methanol will become the leader in the general target market of low-carbon fuel and will become the main fuel for ships (Fig. 1). The total volume of methanol (CH3OH) in the general target market will be 70%, ammonia (NH3) at 11%, liquefied natural gas (LNG) at 9%, and hydrogen (H2) at 4%, other fuels contributing approximately 6%.
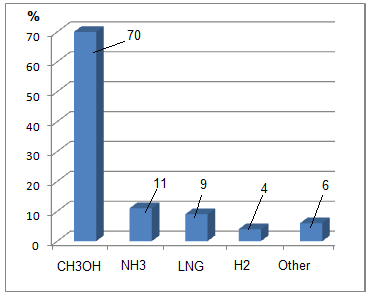
Figure 1 Projected state of the low-carbon fuels market in 2050 [34]
Slika 1.Projekcija stanja na tržištu goriva s niskim udjelom ugljika za 2050. godinu
3. USE OF METHANOL IN MARINE ENGINES / Korištenje metanolom pri brodskim motorima
Nowadays, diesel engines with compression ignition are mostly used in shipping [22]. The compression ratio for diesel engines is 1:20. Such compression conditions lead to the self-ignition of heated diesel fuel.
Methanol is characterized by a high octane number and low cetane number. The high octane number of methanol allows its successful use for engines with spark ignition. However, its low cetane number makes using methanol directly in compression ignition engines difficult.
Several solutions have been proposed to remove existing barriers and make marine engines more efficient, such as mixing methanol and diesel fuel [5], adding ignition accelerators [35], and using dual-fuel technology [32].
In [36] it is reported that when using diesel fuel mixed with methanol and water, emissions of nitrogen oxide and soot are reduced, and the economic characteristics of the engine are also improved. Nevertheless, there are certain restrictions on obtaining fuel mixtures, and the main one is that the ratio of methanol to diesel fuel should be low to avoid a negative impact on the engine operation process [37]. Besides, the presence of water in some cases can lead to the separation of the mixture into watermethanol and diesel phases [5]. It is also necessary to consider that diesel fuel and methanol have different properties. For their mixing, it is necessary to use co-solvents, which have a rather high cost. Therefore, further research is needed to reveal the full potential of using methanol for the direct mixing method.
The use of ignition accelerators also has some disadvantages. Ignition boosters usually consist of nitrogencontaining compounds, such as tetrahydrofurfuryl nitrate and octyl nitrate. These compounds are considered toxic [38].
The next solution option is the use of dual-fuel technology. Dual-fuel technology involves the use of two types of fuel: diesel fuel and methanol. Diesel is characterized by a high cetane number, so it is used for ignition. Methanol has a low octane number and is ignited by diesel fuel. To improve the operation of dualfuel engines running on methanol, it is necessary to modernize the fuel supply system, cylinder heads, and injectors. Herewith, there is no need to modify the engine internally [25].
The system of operation of dual-fuel engines has the following implementation options: methanol injection through the port and direct methanol injection [38].
When implementing the first option, methanol is fed to the inlet, where it forms a combustible mixture with air, and then diesel fuel is fed directly into the cylinder near the top dead center. After that, as a result of the self-ignition of diesel fuel, the mixture of methanol and air ignites. However, the significant latent heat released during evaporation significantly lowers the inlet temperature. This effect can create difficulties during a cold start of the engine or cause it to stall at idle speed [39].
Another version of the dual-fuel engine includes direct injection of methanol as well as diesel fuel into the cylinder. Direct injection involves the use of two separate systems for supplying methanol and diesel fuel. In this case, methanol as the base fuel is used alongside a small amount of diesel fuel, which acts as a starter [40]. While the engine is running, the injection parameters of both diesel fuel and methanol are controlled using a special control unit. Using this design makes the engine last longer, use less fuel, and reduce harmful emissions [37,41].
Currently, marine diesel engines using methanol as fuel are already commercially available. Since 2016, the Methanex company, together with its Waterfront Shipping division, has been operating and bunkering dual-fuel vessels on methanol. They are now world leaders in the use of methanol for ocean tanker engines. It is reported that soon about 60% of their fleet will be able to run on methanol [42].
The ferry Stena Germanica is also an example of the successful use of methanol as a motor fuel. The ferry's engine was originally configured to use two types of fuel: diesel and methanol. After a long period of operation, in 2021, modernization took place and now the ship operates entirely on methanol [43].
Two new vessels with a deadweight of about 50,000 tons have been commissioned by Stena Bulk, which will operate on dual-fuel engines powered by methanol. Onshore research projects are also focused on engines running on both methanol blends and pure methanol.
A. P. Moller-Maersk, the world leader in container shipping, has invested about US$7 billion in marine vessels that use methanol as a motor fuel. In the first quarter of 2024, the company plans to build eight dual-fuel ocean vessels with a capacity of 16,000 containers each. Implementation of the presented measures will significantly reduce emissions of carbon dioxide and other harmful substances [45,46].
Engine manufacturers, especially MAN and Wartsila, played a central role in the design and construction of these vessels. Both continue to research and develop engine technologies to support a potential transition to an environmentally clean fuel — methanol [47].
For example, MAN Energy Solutions plans to release the MAN 175DF-M high-speed dual-fuel engine by the end of 2026. The engine will be optimized to achieve the highest methanol fraction and the best efficiency for various purposes. In the case of using “green methanol”, the carbon emissions of the MAN 175DF-M engine will be reduced to zero [48].
The main strategic direction of Wärtsilä's development is the decarbonization process, which is confirmed by significant capital investments in the development of new engine designs.After the introductionof the Wärtsilä 32 engine, the company is developing four more new engines that will be able to run on methanol fuel [49].This approach expands the supply of methanol engines to the market for a variety of vessel types and brings the maritime industry closer to achieving its 2050 carbon-neutral goals.
Fuel cells for marine vessels running on methanol are currently in the pilot project stage. The ferry MS Innogy is the first ship in Germany to use fuel cells and run on methanol. The purpose of the ferry was to demonstrate the great potential of methanol fuel. The result was achieved thanks to the cooperation between SerEnergy and Innogy [50]. The design of methanol fuel cells is presented in the form of a modular unit, which is a unique design solution. The power source as a whole consists of fuel cells and a battery. Fuel cells perform the function of a stroke extender, thanks to which the ship can cover longer distances without refueling.
Rational use of spent heat in fuel cells allows for high coefficients of electrical efficiency in the range of 40–50%.
Currently, any type of methanol can be used as motor fuel in marine transport. Despite the creation of various production technologies and the use of various raw materials, the growth of the use of renewable “green methanol" as a motor fuel in the marine sector, remains a serious problem related to the shortage of its production and availability in the necessary volumes.
Therefore, it is relevant to study the possibility of increasing the production and use of green methanol as an economically reasonable and efficient alternative source of energy, which could be compared with traditional types of fuel and at the same time be less harmful to the environment.
4. ANALYSIS OF METHANOL PRODUCTION TECHNOLOGY / Analiza tehnologije proizvodnje metanola
Most methanol is currently produced from non-renewable natural sources, such as natural gas (“gray methanol”) as well as hard coal (“brown methanol”), mainly for economic reasons [51,52]. Global methanol production capacity was 164,000,000 tons in 2021 and has grown steadily at 10% annually since then. This forecast is also relevant for the next decade [53].
The main industrial methods of obtaining methanol are based on the conversion of synthesis gas. The chemical reaction takes place with the participation of copper-zinc-aluminum (Cu/ZnO/Al2O3) catalysts at a pressure of 5 to 10 MPa and a temperature of about 260 °C [54]. Natural gas is used as a raw material for this technology. At the same time, the process of methanol production takes place at a relatively low temperature, which is why it is also called a low-temperature one.
The process of converting natural gas into synthesis gas in this technology is the most expensive stage. The mixture temperature is 900—1100 °C until the end of the natural gas reforming process. Thus, rational use of heat can significantly increase the overall efficiency of methanol production. In this regard, the improvement of this process has significant prospects. Fig. 2 shows the main stages of methanol production based on natural gas.
Taking into account the methods of delivering natural gas to an enterprise and the constant fluctuation of its price on the stock exchanges, especially recently, alternative types of fossil resources such as coal are used to obtain methanol [55,56].
An important technical method of obtaining methanol is the process of converting coal into methanol. All existing coal-methanol plants use coal gasification to obtain syngas. However, this process is associated with high CO2 emissions and low energy efficiency, with a low methanol yield [57].
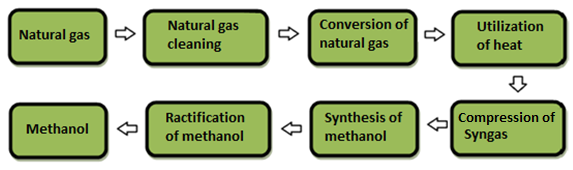
Figure 2 The main stages of methanol production based on natural gas
Slike 2. Glavne etape proizvodnje metanola temeljene na prirodnome plinu
Methanol, which is obtained from fossil raw materials, is a low-carbon fuel. The increasingly critical need for low-carbon fuels for the energy transition leads to a growing interest in renewable methanol production, which was proposed in the early 2000s by George Olah [58]. It is to be noted that the current widespread use of fossil methanol as a fuel may also facilitate a gradual transition to renewable forms of methanol, given that the distribution and transportation infrastructure will remain intact.
Captured carbon dioxide as well as “green hydrogen” can be used to produce renewable methanol. In this case, the finished product is called “green e-methanol". Biomass can also be used as a renewable feedstock for methanol production. Then the obtained product is called biomethanol. Methanol produced by any of these methods is chemically similar to the production of methanol from fossil fuels.
Currently, only a few plants produce less than 200,000 tons of renewable methanol annually. Existing commercial renewable methanol plants use waste and by-products from other industries as raw materials. This approach is still the most cost-effective [52,59].
The first modern industrial plant for the conversion of carbon dioxide into methanol using local, low-cost geothermal energy operates in Iceland [60]. This commercial demonstration plant has a capacity of 4,000 tons of methanol per year. The methanol production technology involves the conversion of geothermal CO2 and green hydrogen at the expense of cheap geothermal energy [61].
E-methanol is an interesting fuel for the transportation sector because it is quite clean and allows for the same storage and distribution infrastructure as traditional petroleum fuels [62].
The establishment of industrial production of electronic methanol largely depends on the availability of cheap raw materials such as “green hydrogen” and carbon dioxide, as well as on the amount of capital costs for the construction and start-up of the plant. The main factors affecting the cost of finished products are the price of the energy needed to produce the required amount of “green hydrogen" and the utilization rate of equipment (especially electrolyzers). Currently, the cost of methanol obtained in this way is quite high.
Synthesis gas obtained as a result of biomass gasification, which is used for the synthesis of “green methanol", is a relatively new method. Furthermore, to utilize synthesis gas in existing methanol productions, it is imperative to purify and enhance it [63,64].
The main processes of methanol production from biomass are as follows: preliminary preparation of raw materials, gasification, gas purification, gas conditioning, synthesis, and purification of methanol [65]. The use of renewable energy sources for the synthesis of methanol is beneficial from the point of view of reducing global emissions into the environment. Fig. 3 shows the main stages of methanol production based on biomass.
In this case, the scale of biomethanol production will depend on the availability of cheap biomass. The production of biomethanol requires a reliable and stable supply of raw materials. While in some cases the supply of biomass can be done on-site, larger projects require much more complex feedstock supply chains. It is worth noting that since biomass has the potential to be used in a wide range of energy purposes and for materials production, biomethanol production will compete with other applications. For this, biomass must be obtained from sustainable sources.
To meet the growing demand for methanol, methods of its production from fossil raw materials are being improved and new methods of production from renewable sources are being developed, which, if commercialized, could have significant environmental benefits.
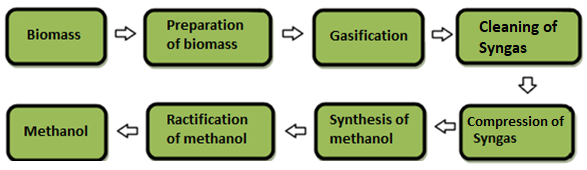
Figure 3 The main stages of methanol production based on biomass
Slika 3. Glavne etape proizvodnje metanola temeljene na biomasi
The economic component in production planning is decisive. Setting a benchmark in this case may only be valid for a certain, relatively short period due to unpredictable fluctuations in fuel prices. Such an approach would only be useful for shipowners to help them make responsible choices of fuel type. Comparative characteristics of the cost of methanol produced from different types of raw materials are given in Table 1.
Table 1 Cost of methanol production
Tablica 1. Troškovi proizvodnje metanola
Type of raw material | Cost of methanol production in USD/t | References |
---|---|---|
Natural gas | 100 - 300 | [52] |
Coal | 140 - 250 | [55,66] |
Biomass | 215 - 770 | [67,68,69] |
e-methanol | 800 - 1600 | [70] |
Table 1 shows that the cost of methanol production from natural gas is about 100 USD/t for territories rich in natural gas, where its price is the lowest, namely North America and the Middle East. It is 300 USD/t for the countries of the European Union [70]. While the cost of methanol production from coal, which is almost entirely based in China, ranges from 140 to 250 USD/t [55,66].
To obtain renewable e-methanol, the most advanced method is a combination of electrolysis of water with the production of H2 and subsequent catalytic synthesis of methanol from CO2 captured from exhaust, smoke gases, or the air. The cost of e-methanol produced in this way largely depends on the cost of the raw materials: H2 and CO2. According to Table 1, the cost of production per ton of methanol ranges from $800 to $1,600.
The cost of production of ecologically clean hydrogen primarily depends on the combination of further reduction of costs for the production of electricity from renewable sources and electrolyzers and an increase in the efficiency of production processes. It is expected that with the predicted reduction in RES prices, the cost of electronic methanol will decrease to the level of 250—630 USD/t by 2050 [52].
It should also be noted that, as in the example of companies that use natural gas to produce methanol, some economies of scale must be achieved. Economies of scale will reduce the cost of e-methanol produced in large plants.
According to Table 1, the production cost of methanol from biomass is lower than that of electronic methanol. However, in most cases, it exceeds the costs of “gray methanol” obtained from coal and natural gas. And though shortly the production of “green methanol" may become economically profitable alongside the availability of large volumes of biomass and derivative materials in large amounts, the global energy needs will not be satisfied.
The techno-economic analysis of methanol production shows that the strengths of the methods considered can be combined to create a new, more efficient technology. One promising option could be the joint use of renewable and fossil raw materials. After some time, it will be able to technically improve the production of methanol, make it environmentally friendly, and increase the use of renewable sources [72].
5. NEW TECHNOLOGY OF METHANOL PRODUCTION / Nova tehnologija proizvodnje metanola
Based on the conducted research, we have created a new technology for the production of methanol, which involves the processing of natural gas and biomass at the same time. Fig. 4 shows the main stages of joint production of methanol from biomass and natural gas.
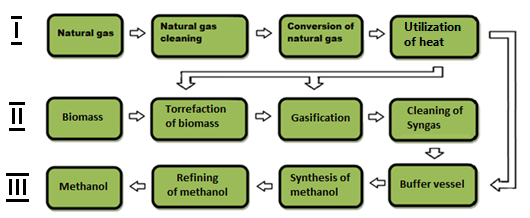
I – the first technological line; II - the second technological line; III – the third technological line
Figure 4 Main stages of joint production of methanol from biomass and natural gas
Slika 4. Glavne etape zajedničke proizvodnje metanola iz biomase i prirodnoga plina
The set of equipment for the production of methanol involves the use of three technological lines. The first technological line converts natural gas into synthesis gas. The second technological line is designed to obtain synthesis gas from biomass. On the third technological line, the synthesis gas flows are mixed, and methanol is factually produced.
The process of autothermal reforming (ATR) is used for the production of synthesis gas on technological line “I” [73]. The peculiarity of the process is that the necessary heat is generated directly inside the reformer (Fig. 5) through the exothermic reaction of burning natural gas into oxygen reaction — (1), which occurs at a high temperature: 1100–1450° C. After that, steam reforming reactions (2) and shear conversion (3) take place in the presence of a catalyst. At the exit from the reactor, the temperature of the formed synthesis gas ranges from 950 to 1100° C [74,75].
CH4 + 0.5O2 = CO+2H2O (1)
CH4 + H2O = CO +3H2 (2)
CO + H2O = CO2 + H2 (3)
Synthesis gas obtained by the presented process has a high content of carbon monoxide, which gives it high reactivity. Therefore, the stoichiometric module of synthesis gas M, determined by equation (4), is in the range of 1.7–1.8, which indicates the presence of hydrogen deficiency in its composition [73]. For the production of methanol, the stoichiometric module must be brought to a value equal to 2 [76].
M = (H2 - CO2) / (CO + CO2) (4)
Under the conditions of the new technology, the adjustment of the stoichiometric module is carried out by mixing synthesis gas obtained as a result of natural gas reforming and hydrogen-rich synthesis gas obtained from biomass.
In this technological scheme, we partially or fully use the heat obtained in the process of autothermal reforming to obtain gas synthesis from biomass on the technological line “II”.
Both conducted research [73,77] and production experience indicate that due to the captured heat during the ATR process, it is possible to increase the productivity of the enterprise by 25—30%.
Synthesis gas is obtained from biomass using torrefaction and gasification processes.Torrification is an energy-efficient process of converting biomass into a carbon-enriched substance by heating it to a temperature of 200 to 300° C.As a result, the raw material loses about 30% of its mass and only about 10% of its energy. Thus, the energy density of the resulting solid residue increases by approximately 30% [14]. This course of the process indicates one of the fundamental advantages of the torrefaction process, which is the high degree of transfer of chemical energy from the raw material to the liquefied product. Due to this, the properties of the obtained fuel are improved.
During research on the torrefaction process, we established that a thermal effect occurs within the temperature range of 250—300° C, which is manifested by an additional increase in the temperature of the processed biomass by 8—10%. In our opinion, this phenomenon can be explained by the passage of exothermic chemical reactions during the thermal decomposition of biomass. Thanks to the established effect, it is possible to reduce the amount of external heat required for the torrefaction process by 8—10%. Therefore, based on the above research results, we use torrefaction temperature regimes in the range of 250-300°С for the realization of the developed technology.
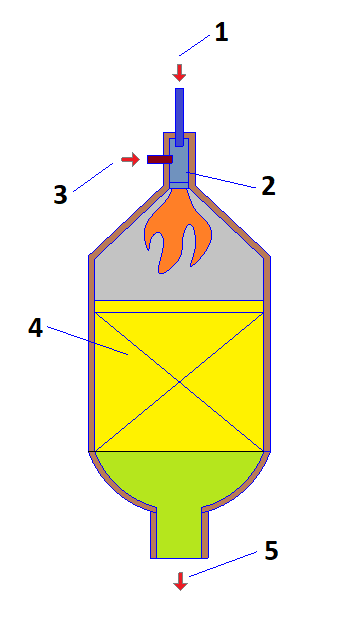
1–Oxygen; 2– burner; 3 – natural gas; 4 – catalyst layer; 5–synthesis gas.
Figure 5 Autothermal reformer
Slika 5. Autotermalni reformator
After the completion of the torrefaction process, biomass gasification takes place. The torrefied biomass is mixed with the sorbent CaO (calcium oxide) in the specified mass ratios and fed into the reactor for gasification. When the temperature reaches ﮿ 700 C, water vapor is supplied to the gasifier. After that, the gasification of the torrefied biomass with water vapor begins, and the generated synthesis gas is withdrawn. According to the data of our research, which correlates with the data of the work [203], it is precisely at a temperature of 700° С that the action of the sorbent is optimal.
In a simplified form, the gasification process can be described using the following chemical reactions: water gas reaction (5), water gas shift reaction (3), Boudouard reaction (6):
C + H2O = CO + H2 (5)
C + CO2 = 2CO ( 6)
Therefore, calcium oxide CaO, by the carbonization reaction (7), acts as a sorbent for the absorption of carbon dioxide CO2 with the formation of calcium carbonate CaCO3. As a result of a decrease in the partial pressure of CO2, the reaction of the water gas shift (3) towards the formation of hydrogen increases.
CaO + CO2 =CaCO3 (7)
Since the carbonation reaction of CaO is exothermic, the heat released facilitates the endothermic gasification process. Establishing quantitative characteristics of heat release requires additional research.
The conducted studies established that for different types of biomass and different mass ratios of CaO sorbent and steam to torrefied biomass, as well as the equipment used, the hydrogen content in synthesis gas can reach up to 82% [79-83].
In our case, in addition to the torrefied biomass, the gasifier can be supplied with enriched gas, which is released during the torrefaction process (pyrolysis gas). The addition of pyrolysis gas has a positive effect on the efficiency of the gasification process as a whole. Also, if necessary, the obtained mixture of gases at the exit from the gasifier can be enriched with "green hydrogen" [60].
It is necessary to note that the CaO sorbent loses its chemical activity in the process of operation, so after a certain time it is necessary to regenerate it. One of the methods of regeneration is the calcination of spent CaO by burning unreacted torrefied biomass. After the regeneration process, the restored calcium oxide returns to the gasifier.
In this case, in addition to effective disposal of the remains of unreacted torrefied biomass and obtaining additional heat, which enters the gasifier together with the burnt sorbent, carbon dioxide is released in its pure form. Pure carbon dioxide is separated in the process of calcium oxide regeneration and is stored in an additional tank. Then it can be used for various technical and commercial purposes.
The peculiarity of the process of obtaining synthesis gas from biomass on technological line "II" is that it is optimized by reducing the use of heat for torrefaction to 10%, and the energy required for it is covered by the residual heat obtained during the conversion of natural gas.
The obtained synthesis gas undergoes purification and is fed to the buffer tank included in process line "III", where it is mixed with synthesis gas obtained from natural gas. When the stoichiometric module of the synthesis gas mixture M is equal to 2, it is sent for the formation of methanol.
The synthesis of crude methanol is carried out at a pressure of 5.0 MPA and a temperature of 200 – 270° C using a catalytic process. Next, the crude methanol is distilled, and the water produced during the synthesis and any by-products are removed.
Production of methanol from natural gas can be considered the cheapest solution in most cases. However, the cost of fossil fuels can vary depending on some factors, such as geopolitics [85]. Also, today, one of the important factors that affect the prices of natural gas and the possibility of its supply is the conduct of hostilities in the area where gas pipelines are located [86].
The paper [69] provides data on the cost of methanol produced from natural gas and biomass at different enterprises. In this case, the cost of methanol produced from natural gas is higher and amounts to $250 per ton, while the cost of methanol produced from biomass is lower and amounts to $220 per ton. The reduction in the cost of methanol produced from biomass occurred due to cooperation at its production with an existing enterprise – a pulp and paper mill. According to the authors [87,88], in the case of the cooperation of enterprises involving waste heat usage, methanol prices would decrease for various production conditions by 10% to 35%.
Currently, a typical world-scale methanol plant using natural gas as feedstock has a production capacity of about 3000 – 5000 MTPD t/day, or 1 – 1.7 million t/year [52]. Even larger plants of 10,000 MTPD and above are expected to further improve the economies of scale in methanol production [73]. The proposed technology can achieve the above-mentioned productivity values, provided there is an established supply of raw materials and appropriate equipment is available. Although its most effective applications can be reached for large-capacity enterprises.
Thus, the conducted research allows us to conclude that the new technology will diversify the raw materials base due to two independent sources and increase green methanol productivity by 30%. New technological solutions make it possible to reduce specific production costs and, under appropriate conditions, to obtain methanol at a lower cost than using each of the methods separately.
6. CONCLUSIONS / Zaključci
1. The advantages of methanol make it a leading alternative fuel now, and in the future, it offers the shipping industry a direct path to decarbonization. In the short term, regular methanol will be able to reduce greenhouse gas emissions from combustion, and in the long term, green methanol could enable the industry to meet the International Maritime Organization's decarbonization targets.
2. A new methanol production technology has been developed, which involves the joint use of biomass and natural gas as raw materials. The advantage of the technology is ensured by the possibility of a guaranteed supply of raw materials, an increase of the enterprise production capacity by 30% due to green methanol, a renewable fuel, as well as reducing the cost of the finished product.
3. Implementation of the developed technology will increase the potential of methanol as an environmentally friendly and competitive alternative fuel for, in particular, the marine industry.
Author Contributions: A. P.: conceptualizationandoriginal draft preparation; M. P.: conceptualizationand original draft preparation; A. S.: data curation and editing; S. K.: data curation and visualization; L. K.: editing and visualization.
Funding: The research presented in the manuscript did not receive any external funding.
Conflict of interest: The authors state that there is not conflict of interest.