1. INTRODUCTION / Uvod
Merchant ships have large amounts of waste heat, which has not been fully utilized yet. However, this issue requires a solution to improve the environmental friendliness and reliability of marine transport.
The main direction of heat waste recovery on ship boards that are under study to date is the utilization of an organic Rankine cycle for the production of electricity by recuperation of heat from engine exhaust gases and/or jacket cooling water [2,3].
There are researches where it is proposed to use a heat pump to increase the temperature potential of the engine jacket cooling water thermal energy [4] or low-pressure steam [5]. As a result, it is possible to obtain water steam at pressures of 0.3-0.9 MPa, which will be used for sanitary and technological needs. However, heat pumps with a high heat sink temperature (about 133 °C) are currently not available on the market [6].
Less attention is paid to the introduction of onboard heat-driven refrigeration machines, although this direction is also promising [7,8].
There is a strong irregularity in the production and consumption of the on-board waste heat [5]. A lot of fuel is consumed while the ships are at the port not only for electricity generation, but also for heat generation (heating the potable water, accommodation spaces, and fuel tanks) [1]. For example, container ships with TEU from 0-999 to 20000+ consume the auxiliary boiler power from 250 to 700 kW at berth and anchored vs. 0 kW at sea [1]. At the same time while ships are at sea, the waste heat from engines usually is not fully used because of low demand.
The application of thermal energy storage (TES) systems can increase the degree of waste heat recovery due to smoothing out irregularity in demand and production. This heat can be accumulated in the TES system and used when the ship is at the port.
Application of on-board TES units are still limited for two main reasons, namely, “the huge volume required to store enough energy and the abundant waste heat available on-board, which usually overcomes the heating demand, thus reducing the need to store it” [2]. In the opinion of authors of this study, the second statement is controversial, since passenger and merchant ships have auxiliary boilers for steam generation in port. However, interest in the use of onboard TES has increased in recent years [2,3,9,10], which is explained by the effort to save fuel and reduce GHG emission. For example, in [10], heat recovery of engine exhaust gases was considered for heat accumulation when the ship is at sea; but when the ship is at port (when the main engine is off) the accumulated heat can be used for different purposes. However, large heat exchangers for extracting the heat of recuperation from engine exhaust gases (taking into account the existing exhaust gas boiler (EGB) and TES units of 1000 m3) are difficult to place on a ship. In the study [3] TES units (sensible heat) were proposed to be used for the operation of organic Rankine cycle plant when the ship engine cannot provide this plant with a high-temperature heat source.
Mainly there are three types of TES systems using latent heat, sensible heat, and heat of chemical reaction. The latent heat TES system is more attractive vs. other ones because they inherent high storage density with small temperature swings and isothermal features during charging/discharging periods. However, the main disadvantages are the low thermal conductivity of widespread phase change materials (PCMs) and higher cost per one joule of energy storage. Overcoming the mentioned disadvantage is now being actively investigated, and there are reasons to get good results at a low cost (additives to PCM of carbon nanostructures) [11-13]. Another difficulty that hinders practical application is related to the need for an individual approach to the TES unit design in each specific case, taking into account the energy potential of the heat source.
The purpose of this study is to analyze the feasibility of introduction of the onboard heat-driven ejector refrigeration machine (ERM) with a TES unit. It operates due to utilizing the EGB steam and provides a significant saving of electricity and GHG emission reduction compared with the traditional ship mechanically-driven vapor-compression refrigeration machine (VCRM).
2. DEVELOPMENT OF DESIGN SOLUTION OF THE EJECTOR REFRIGERATION MACHINE WITH TES UNIT / Razvoj rješenja dizajna ejektorskoga rashladnog uređaja s TES jedinicom
The standard single-stage ERM with ejector with a conical-cylindrical mixing chamber that was researched by the authors [14] was taken as the prototype of the onboard heat-driven ERM. The ERM design with two ejectors of different configurations was applied for on-board application, due to the varying in a wide range of refrigerant condensing temperature [15].
As it was shown in [15], one of the problems of on-board heat-driven ERM operation is the irregularity in its supply with waste heat. During ship in port, a source of waste heat (cooling jacket water) is not available, therefore switching from ERM operation to the VCRM operation was recommended [15]. However, using a TES unit can solve this problem and lead to fuel savings.
This paper evaluates the technical possibilities and energy-saving feasibility of utilizing a TES unit for heat power to supply the onboard heat-driven ERM during stays in port. Fig. 1 shows the layout of the proposed concept.
Figure 1 Schematic diagram (a) and a thermodynamic cycle (b) of an onboard ejector refrigeration machine with thermal energy storage unit
Slika 1. Shematski dijagram (a) i termodinamički ciklus (b) brodskoga ejektorskog uređaja za hlađenje s jedinicom za pohranu termalne energije
VCRMs are widely used on ships at present. The main difference between VCRM and ERM is that instead of a compressor that consumes electricity, a generator and ejector are used in ERM. The refrigerant boils due to the supply of the generator with the thermal energy of EGB steam, and an ejector acts as a compressor. It was decided to reject a complete replacement of the generator with TES for the following reasons. Due to the low heat transfer coefficient from PCM to the refrigerant in the TES unit during discharge mode (which will be discussed in more detail below), the heat transfer surface area should be extended. This will contribute to an increase in pressure losses in the refrigerant circuit. Therefore, it was decided to ensure parallel operation of the generator and TES unit. This approach will not ensure the completely autonomous operation of ERM, i.e., it will still need steam from the auxiliary boiler in the port, but will reduce the generator thermal load and, as a result, save fuel.
Two modes of operation of the proposed ERM with a TES unit are described below.
Mode 1 – TES unit charging (ship at sea)
In this mode, the ERM operates using the heat of EGB steam. EGB steam is supplied simultaneously for the operation of ERM (in the generator) and to the TES unit for its charging. Due to the heat transfer to the PCM, the water vapor condenses (PCM melting point is below the temperature of EGB steam). When all the PCM has melted and its temperature begins to rise (sensible heat), the supply of steam to the TES unit is stopped. A charged TES unit can store heat for a long time due to its compact design and the presence of thermal insulation. However, if the ship is at sea for a long time, when there is no need for stored heat, it will be necessary sometimes to “recharge” the TES unit.
Mode 2 - TES unit discharging (ship at port)
In the mode when EGB steam is not generated and steam is produced by the auxiliary boiler, the refrigerant flow (whole or portion) passes through the TES unit. The ERM generator is supplied by auxiliary boiler steam in an amount less than when EGB operates. As the refrigerant passes through the TES unit tubes, it boils at a temperature lower than the PCM solidification temperature. If a series connection of TES unit and the generator is used, then the wet refrigerant vapor boils off in the generator. If a parallel connection TES unit and the generator is used, the refrigerant is divided into two flows, one is completely boiled off in the TES unit, the other boiled off in the generator, and then they are mixed. Further in paper authors considered and analysed only the second option. The diagram in Fig. 1 is given for the parallel connection option of the TES unit and the generator. It should be researched and determined in future which operation mode is preferable. When the latent heat of the PCM has been transferred to the refrigerant and the PCM is solidified, the refrigerant flow will be completely switched to the generator.
3. THERMAL ENERGY STORAGE UNIT / Jedinica za pohranu termalne energije
The choice of TES unit design was based on the following:
1. The steam is generated by the EGB while underway on most of the ships. The auxiliary boiler which consumes fuel is operated at port. The introduction of the TES unit into the ERM design will contribute to eliminate or reduce the use of steam from the auxiliary boiler and allow for saving fuel.
2. The weight and size characteristics of the TES unit as part of the on-board ERM should be minimal. It is obvious that the thermal storage capacity of a TES unit is proportional to its size. Thus, an optimization problem should include the following items: the rational mass and size of the TES unit, additional space for new equipment on the ship, additional fuel consumed for TES transportation, and energy resources used for TES manufacturing. The possibility of introduction of the TES unit as part of onboard ERM is considered in the presented study. At this stage of the research, the problem of practical implementation of the ERM with TES unit needs to be resolved in future studies by means of environmental and energy analysis of ship refrigeration equipment [15,16].
Analysis of the TES unit designs [17,18] showed that most of them are designed as a single-flow. In the proposed design of ERM with the TES unit, the hot heat transfer medium (steam from the EGB) will heat the PCM, and the refrigerant will take away heat from the PCM. So, the TES unit must have two circuits for the heat transfer mediums. Among a large number of publications, the TES unit design [19] in Fig. 2 seems to be the most rational, which was taken as a prototype in the present study. In the proposed schematic diagram (Fig. 1), the “CW inlet” and “CW outlet” in Fig. 2 will correspond to the inlet of liquid refrigerant with generating pressure (point 6 on Fig. 1) and outlet of vapor refrigerant with same pressure (point 1 in Fig. 1). Similar, the “GW inlet” and “GW outlet” in Fig. 2 will correspond to the inlet of superheated water steam with pressure 0.5-0.7 MPa and outlet of condensed water with same pressure.
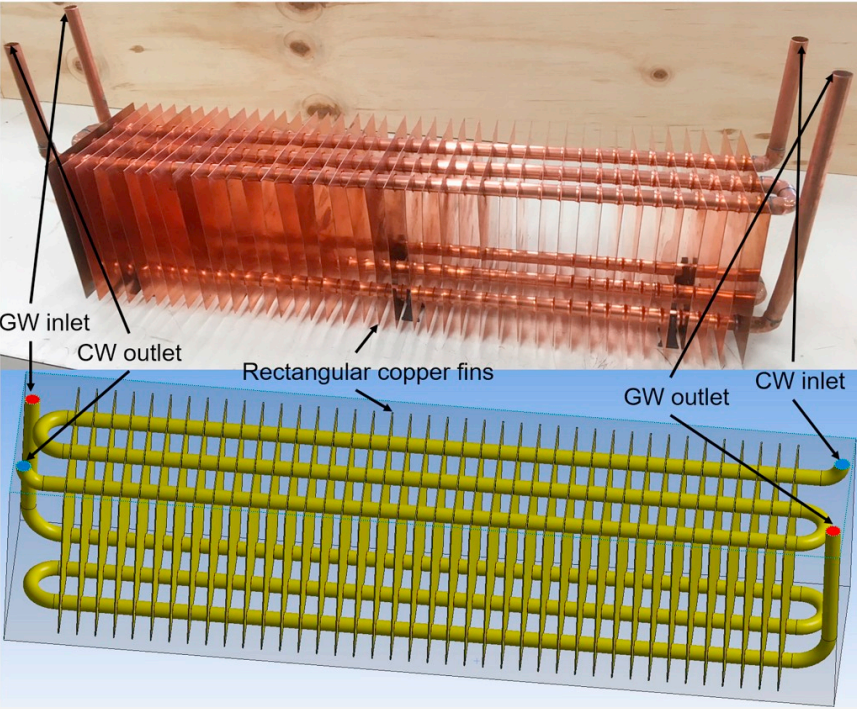
Figure 2 Images of the two-flow TES unit with PCM [19]
Slika 2. Slike TES jedinice s PCM-om
The choice of PCM for TES was based on market availability. The dimethyl terephthalate (DMT, C10H10O4) was chosen as PCM because its melting point is 142 °С. The phase change enthalpy of DMT is 170 J/g, its density is about 1.2 g/cm3. It is also non-toxic and it is produced on an industrial scale for the chemical industry [20].
TES unit tubes and fins are proposed to be made of copper, which is compatible with both steam and refrigerant and has high thermal conductivity. Compatibility with DMT remains to be tested.
The given in [19] (Fig. 2) design solution seems to be rational. However, the authors see the following problem. The heat transfer coefficient from the PCM to the tube surface is significantly lower than from boiling refrigerant to the tubes (up to 10-15 kW/(m2 K) dependig on heat flux [21]). The heat transfer coefficient for condensing steam is even more than for the refrigerant. The heat transfer coefficient from the PCM to the tube surfaces will be different at different stages of the process of PCM cooling and solidification process, as well as PCM heating and melting. In [22] the heat transfer coefficient from the PCM to the heat transfer surface in the TES unit during charging and discharging mode has been measured. Its values varied in the range of 5–250 W/(m2·K), which is relatively low for the heat exchangers. Obviously, the greatest thermal resistance inhibiting heat transfer in the TES unit will be from the PCM to tubes and fins during PCM cooling and solidification. The conduction is the dominant heat transfer mechanism during solidification. During PCM solidification, a layer of solid PCM is formed around the tubes with boiling refrigerants and between fins. PCM solid layer with low thermal conductivity contribute to reduction of heat transfer coefficient between the refrigerant and liquid PCM by increasing the thermal resistance. This will lead to the design of an extended heat exchange surface for the refrigerant, which is undesirable for ERM operation due to increasing pressure losses. This is the biggest problem for the proposed TES unit design, which must first be evaluated and then be solved.
A possible solution may be the reduction of the gaps between fins, as well as the addition of a small amount of carbon nanostructures into PCM to increase its thermal conductivity [11-13]. It is planned to analyze this problem in the future to select a rational solution.
4. INITIAL DATA FOR THE ANALYSIS / Početni podaci za analizu
The system, which is standard for merchant ships - a refrigeration plant for air conditioning system (produced by “YORK Marine”) - was chosen as the base variant for comparison analysis with the developed ERM with TES unit. The general specification of the VCRM for marine air-conditioning systems is presented in Table 1.
Table 1 General specifications for the marine air-conditioning system (Hi Air Korea Co., Ltd) – base system*
Tablica 1. Opće specifikacije za pomorski sustav rashlađivanja (Hi Air Korea Co., Ltd.) – osnovni sustav
Parameter | Characteristics |
---|---|
Refrigerant | R404A |
Cooling capacity | 174.1 kW |
Condensing temperature tC | +42 °C |
Evaporating temperature tEv | +7 °C |
* data was accepted according to the marine air-conditioning system manual
The input data for the thermodynamic analysis of the ERM are given in Table 2. The maximum condensing temperature of the refrigerant was 42 °С (the requirement for marine refrigeration equipment for an unlimited sailing area (Table 1)). Low-pressure steam of 0.5-0.7 MPa from an EGB) was considered as a heat source for ERM. EGBs recover the waste heat of marine diesel engines and they are applied on most ships. PCM of the TES unit can be considered as a “secondary heat transfer medium”. The generating temperature in ERM was taken 120 °С, taking into account the steam absolute pressure of 0.5-0.7 MPa (that correspond the saturated temperature of 152-165 °С).
Table 2 General specifications for alternative ejector refrigeration machine with TES unit
Tablica 2. Opće specifikacije za alternativni ejektorski uređaj za rashlađivanje s TES jedinicom
Due to the impossibility of using fire-hazardous working fluids (except ammonia) in a ship’s refrigeration equipment, the choice of low GWP refrigerants for an ejector refrigerator is quite small. We consider the possibility of utilizing the following refrigerants of a new generation: R1234ze(Z) and R1233zd(E) which have GWP<1 [23].
To evaluate the specific mass of the PCM per 1 kWh of TES capacity the following initial data was assumed:
1. The size of the tubes for refrigerant boiling (the upper tubes of the TES unit in Fig. 2) was taken as 12×1 mm.
2. Taking into account the presence of fins and the possible heat transfer enhancement in the PCM solid phase by introduction of the expanded graphite [11,13], as well as considering the experimental data of the study [22], the heat transfer coefficient was taken as 100 W/(m2·K).
5. METHODS / Metode
The compressor power of the VCRM was estimated at the operation parameters listed in Table 1. The standard technique [24] was applied. Thermophysical properties of refrigerant R404A were taken according to RefProp 10.0 [25].
The determination of the ejector entrainment ratio ω was based on the ejector model with a conical-cylindrical mixing chamber [26] taking into account the thermophysical properties of chosen refrigerants R1234ze(Z) and R1233zd(E) [25]. The energy analysis of the ERM and evaluation of the COPtherm was carried out using a thermodynamic model based on mass and energy balance ratios [26,27].
Comparison of ERM and VCRM was carried out based on the value of annual fuel consumption. The electricity consumption for ERM operation is significantly lower than for VCRM. However, its operation in the port requires additional fuel to produce steam. The reduced consumption of steam from the auxiliary boiler in the port by using saved thermal energy will contribute to the additional fuel expenditures on TES unit transportation.
For comparison of ERM and VCRM, it was assumed that they are installed on a 0–1000 TEU container ship with average distance per voyage lvoyage=650 nm, the average duration of cargo voyage τvoyage=6 days, the annual number of cargo voyages 49 [29]. The average time of stay in port τport=1 day. Obviously, ships with long voyages and long stays in port will require a larger TES unit capacity than it is proposed in this study. The main ideas of the approach used here for the analysis are described in detail in [15].
Fuel consumption for the electricity production for the operation of the ERM and VCRM (for one voyage):
MElFuel=Pel∙gF∙(τvoyage+ τport)∙nτ, (1)
where Pel is the electrical power, kW; gF is the specific fuel consumption of a diesel generator, kg/kWh (taken gF =0.23 kg/kWh [15]); τvoyage is voyage duration, hours; τport is duration of staying in port, hours; nτ is operating time factor of the refrigeration system (taken nτ=1).
Fuel consumption for the steam generation for ERM in port (for one stay in port):
MHeatFuel=Pheat∙ηAB∙ τport∙nτ/Qfuel, (2)
where Pheat is the heat power of the generator, kW; ηAB is auxiliary boiler efficiency (taken 80 %); Qfuel is the lower heating value of fuel, kJ/kg (taken Qfuel=42000 kJ/kg).
Fuel consumption for transport of the additional equipment – TES unit (for one voyage):
MTrFuel= AFC∙mEq∙lvoyage, (3)
where AFC is the annual average fuel consumption for the transport of one ton of deadweight per one nautical mile, g/(Dwt·nm) (taken 2.026 (g fuel)/(Dwt·nm) [15]); mEq is mass of the TES unit, ton; lvoyage is distance per voyage, nm.
6. RESULTS AND DISCUSSION / Rezultati i rasprava
To evaluate the compressor power of VCRM and generator capacity of ERM, the air-conditioning cooling capacity of 174.1 kW was taken. Parameters, given in Tables 1 and 2 were used for analysis. Standard methods of thermodynamic analysis for VCRM and ERM [24,26,27] were applied. Additionally, using these methods the values of COP for VCRM with R404А and COPtherm for ERM with R1234ze(Z) and R1233zd(E) were obtained. Thermodynamic analysis of utilizing the R1234ze(Z) and R1233zd(E) in the ERM was performed and resulted in some advantage in the COPtherm of the first refrigerant over the second: 0.263 vs. 0.258 at parameters, given in Table 2. Therefore, the refrigerant R1234ze(Z) was taken for further analysis.
The compressor power and COP for VCRM are given in Table 3. The thermal COPtherm values, as well as the generator thermal capacity for ERM with R1234ze(Z), are given in Table 3.
It is necessary to take into account the electricity consumption of the refrigerant feed pump and the increase in electricity power of the condenser cooling water pump during the ERM operation compared to the operation of VCRM. Therefore, the calculation of the power of these pumps has been additionally performed using the mass flow rates of refrigerant and cooling water (obtained from thermal balance equations). The efficiency of 0.5 for the gear feed pump for low viscous liquids [30] and 0.8 as average value for centrifugal pump for cooling water were taken. Тhe pressure difference between the generator and the condenser was used (Fig. 1) for calculation of the power of the refrigerant feed pump. The hydraulic losses in the plate heat exchanger-condenser were used for calculation of the additional power of the cooling water pump. The increase in water pump power relative to VCRM was determined tentatively since it will depend on the condenser design and it requires further clarification. The calculated values of pumps power are given in Table 3.
The authors evaluated the TES unit weight and size, which would provide storage of thermal energy necessary to replace half of the generator load for 1 day. The half of the generator power (330.5 kW) in heat balance equation was used. The weight and size characteristics of the TES unit are given in Table 3. Refrigerant pipe length in TES unit per 1 kW of generator heat capacity was evaluated from the heat transfer equation. The initial parameters for these calculations are given in section “Thermal energy storage unit”.
Using the equations (1) – (3), the calculation of energy characteristics and annual fuel consumption for VCRM and ERM with and without TES unit was performed. The results of the calculation are given in Table 3.
Table 3 Comparison of energy characteristics for VCRM and ERM
Tablica 3. Usporedba karakteristika energije za VCMR i ERM
As it can be seen from the results presented in Table 3, the operation of ERM without TES unit does not reduce the fuel consumption (within uncertainty of obtained results) for the operation of air-conditioning system in comparison with VCRM. Annual fuel consumption for the operation of VCRM is 81225 kg vs. 80567 kg for ERM – Table 3. This can be explained by the fact that the fuel consumption for auxiliary boiler heat generation during ERM operation in port approximately equals the fuel savings when ERM operates using waste heat during the voyage. However, this conclusion is valid for 0–1000 TEU container ship. It is expected that for ships with a long voyage duration and infrequent stays in the port, the utilizing of the ERM will be more expedient than VCRM.
At the same time, the lower fuel consumption is inherent in ERM with TES unit for its operation compared to the traditional VCRM: 53916 vs. 81225 kg of fuel per year. This encouraging result was obtained taking into account the following two aspects:
a) the fuel was consumed for transportation of ERM with TES unit;
b) the fuel was consumed for production of half required heat of ERM generator during staying in port.
Therefore, the authors made the conclusion that the proposed in this paper scheme of ERM with TES unit is promising for marine application. In authors’ opinion, the more detailed analysis, design, construction and experimental study of ERM with TES unit is a current issue.
7. CONCLUSION / Zaključak
A novel ejector heat-driven refrigeration machine for an onboard air-conditioning system of a merchant ship was conceptualized and analyzed. The following conclusion can be formulated based on the results obtained:
- ERM operated with eco-friendly refrigerant R1234ze(Z) at a condensing temperature of 42 °С, evaporating temperature of 7 °C and using as a source of heat the steam from exhaust gas boiler of 0.5-0.7 MPa provide the COPtherm=0.263;
- for decreasing ERM demand in steam from auxiliary boilers during the staying in port, the introduction of a TES unit with PCM with a melting point of 142 °C was proposed; the TES unit volume and mass that provide storage of thermal energy necessary to replace half of the generator load for 1 day were 16.5 ton and 125 m3 at ERM cooling capacity of 174 kW;
- ERM with TES unit is inherent the lower fuel consumption for its operation compared to the traditional VCRM: 53916 vs. 81225 kg of fuel per year;
- utilizing the onboard ERM without a TES unit does not provide significant fuel savings over traditional VCRM: 80567 vs. 81225 kg of fuel per year;
- it is advisable to use the proposed ERM with a TES unit on ships that have short voyages and frequent stays in port.
Based on the carried-out research, the authors formulated tasks that require further solutions:
- to analyze the heat transfer coefficients during cooling and solidification of PCM in the TES unit using CFD modeling;
- to evaluate the feasibility of various heat transfer enhancement methods in the TES unit during PCM solidification;
- to solve the optimization problem of rational TES unit mass and sizes for various types of ships with different durations of voyages and staying in ports;
- to evaluate the rational portion of the thermal load of the ERM generator that can be replaced with the heat from the TES unit for various types of ships with different durations of voyages and staying in ports.
Author Contributions: K. Shestopalov: conceptualization, methodology, validation, investigation, editing and review; O. Konstantinov: investigation, formal analysis; V. Ierin: investigation, review, formal analysis, O. Khliyeva: supervision, conceptualization, methodology, formal analysis, writing – original draft.
Funding: The research presented in the manuscript did not receive any external funding.
Conflict of interest: None.
Acknowledgement: The authors acknowledge the facilities, scientific and technical support from Department of Ship Auxiliary Plants and Refrigeration Equipment, National University “Odessa Maritime Academy”.