1. INTRODUCTION / Uvod
Shipyards are divided into two categories according to the work they do: construction and dismantling. While construction shipyards are comprehensive industrial centres where a ship is produced from scratch, dismantling shipyards are facilities where the useful parts of the ships that have completed their life are broken down and sent for recycling. Shipyards have large-scale industrial infrastructure and both production and dismantling processes cause large-scale environmental damage. For this reason, international organizations such as the International Maritime Organization (IMO) and the European Union (EU) and the academic community have carried out many studies to reduce the environmental impact of shipyards. In addition to the environmental damage, shipyards have important technical and economic infrastructure as large enterprises where large amounts of raw materials are processed (or recycled). In addition, the processes carried out in the shipyards also pose great risks in terms of occupational health and safety, and the relevant regulations are regulated by the International Labour Organization (ILO) and the U.S. Conducted by the Department of Labour Occupational Safety and Health Administration (OSHA). The financial, economic and technical infrastructure and activities of the shipyards are determined according to the market conditions and are not the subject of an overarching policy as they vary according to the country, institution and time.
Within the scope of this study, international legislation and scientific literature on environmental, economic and technical impacts originating from the shipyard were examined chronologically under three headings (international legislative framework on environment and occupational health, ship recycling and dismantling, shipyard environmental interaction). The scope of the studies on shipyards was determined as the research question of this study.
2. LITERATURE REVIEW / Pregled literature
This part consists of three sub-titles. In the first sub-title, the basis of scientific studies has been introduced by presenting the international legal framework related to the operation of the shipyards, their environmental effects and occupational health issues. In addition, scientific studies examining and questioning this legislation are also included in this sub-title. In the second sub-title, the studies on recycling and dismantling are examined, and in the third sub-title, the publications on new shipbuilding shipyards are summarized.
The classification of the examined publications was carried out according to the keywords in the titles. In addition to international legislative texts, publications based mainly on legislative review are under title 2.1; publications with words related to recycling and/or disassembly in title 2.2; the publications that directly investigate the effects on the environment and/or human health are evaluated under title 2.3. Although some publications have content that can be examined under different headings, the dominant target of the publication has been prioritized and the classification has been made accordingly.
2.1. International Legislation on Environment and Occupational Health / Međunarodno zakonodavstvo u području okoliša i zaštite zdravlja na radu
Shipyards must carry out their processes in accordance with many national and international regulations. This legislation creates an upper framework for the shipyards to be carried out in a more environmentally friendly, more efficient manner and to respect the rights of workers. In this section, a comprehensive compilation of past and current legislation has been made.
Ships that have reached the end of their life and are no longer needed are scrapped. Various equipment in it is separated for use in other areas. The steel of these ships is cut in the dismantling shipyards and sent to the steel processing factories. This process must be carried out properly so that the steel can be recycled, the demand for steel raw material is met and many people are employed. The most important problem in this application is the emergence of tons of harmful waste such as asbestos, ammonia, chlorofluorocarbons, oily residues, and lead in the shipbreaking business. This affects the health of the workers in the shipyards where the dismantling is done and causes the water resources near the dismantling shipyard to be polluted. On this issue, IMO met with the Secretariat of the Basel Convention (SBC) and The International Labor Organization (ILO) and held international negotiations addressing the issues related to shipbreaking [1]. Argüello Moncayo, examined Basel Convention, Hong Kong Convention and European Regulatory for ship dismantling and recycling in his study. The study analyses the rationale behind separating ship recycling from the waste regime. As a result of the study, it is stated that unless the difference between waste and recycling is determined, ships that have reached the end of their life will continue to follow the "path of least resistance" [2].
The Basel Convention was the first attempt to standardize ship recycling procedures in the international arena. However, the Basel Convention is not directly related to ship recycling but is an international convention established for the cross-border transport of hazardous waste and their disposal. The Basel Convention, adopted in 1989, entered into force in 1992. Due to the practical and legal difficulties in the implementation of the Convention on ship recycling, the IMO was invited to the meetings, and studies for new legal regulations were initiated. The first studies by IMO were carried out in 1998 by the Marine Environment Protection Committee (MEPC) to minimize the damage to the environment during the dismantling of ships that have completed their service life and the transportation of waste harmful to the environment. Along with the studies developed over time, IMO has incorporated the Basel Convention's studies on ship recycling facilities called "Industry Code of Practice on Ship Recycling" and ILO's studies on working conditions in these facilities. MEPC started its work with the draft submitted by Norway in 2006 and adopted the Hong Kong Convention on May 15, 2009 [3].
The Hong Kong Convention consists of four main parts and twenty-five rules. The first part lays down general provisions, the second part the procedures for the building, operation, maintenance, repair and preparation of ships for recycling, the third part the necessary conditions for ship recycling facilities, and the fourth part defines the rules about the reports to be prepared after the ship recycling [4,5]. The Convention has specified in detail the rules it has determined at every stage of ship recycling. The criteria to be determined before the recycling phase should be whether the materials used in the building process of the ship do not contain hazardous waste, and if so, what these substances are, and whether the cargo carried by the ship and their residues on the ship contain hazardous materials. Before the ship is dismantled, all this information, together with its details, should be given to the facility where the ship will be recycled. In addition, ships should be continuously inspected not only when they are to be recycled, but also during construction, operation, and maintenance as if they could be recycled any time. How and under which conditions are the certificates of conformity to be given to the ships after the inspections, the form of the documents (in which language they should be written) and the validity period are specified in detail in the rules determined by the Convention. Recycling facilities to be authorized by the countries party to the Commission are obliged to take measures that will not put the people working at the facility and the environment near the facility at risk. It is within the framework of the rules to carry out degassing for hot processes to be carried out in recycling facilities, and to take the necessary measures to eliminate situations that may cause fire and explosion.
It is a possible danger that harmful substances such as oil and sludge are mixed with sea water during the dismantling of ships carrying harmful cargo such as oil tankers. The heavy metals that come out during the dismantling of the ships can increase in time and become lethal for sea creatures and humans. For example, chromium (VI), with a concentration above 10 ppm in water, is lethal to marine life. The paint residues that come out during the dismantling of the ship have a pungent smell and are explosive. Polychlorinated biphenyls produced during disassembly are one of the materials that cannot be easily degraded. When marine organisms are exposed to this waste, polychlorinated biphenyls will increase cumulatively in the food chain, causing marine life to die. When dismantling the cooling systems, power equipment and equipment used in the transport of dangerous goods on the ship, strict procedures should be applied to prevent the harmful wastes from these materials from spreading to the water and the environment [3]. Alam and Faruque, examined the legal regulations in Bangladesh, which is one of the places where shipbreaking is done most intensively. In this study, the international regulations for the shipbreaking industry were also examined and compared with the legal regulations in Bangladesh. As a result of the study, it was concluded that the shipbreaking laws in Bangladesh should be rearranged and based on the Basel Convention [6]. According to the IMO Guidelines, ships should also minimize their hazardous waste during the design, building, operation, and maintenance phases. Steel, which is the most used raw material in shipbuilding, can be recycled and used in many industries. However, not only steel but also materials used in many parts of the ship such as generators, lighting and batteries are recycled. During recycling, the harm to humans and the environment should be minimized. IMO Guideline 5 also provides details on the Green Passport, which provides information on potentially harmful substances used during the ship's building and on its equipment and systems. IMO provides guidance in areas such as the compliance of the facility to be dismantled with the determined national and international rules, the health and safety of the personnel working in the ship dismantling process, the provision of gas-free certificate to the ship to be dismantled, and the identification of dangerous areas.
The European Waste Shipment Regulation is also based on the Basel Convention. The ship to be scrapped according to this regulation cannot be exported to other non-OECD countries for dismantling. According to the decision of the European Parliament, which was implemented in April 2013, European ships should only be recycled at facilities registered in the European recycling facilities list [6]. In the circular published by the European Commission in April 2022, the names of the facilities currently registered to the union, method of recycling, type and size of ships that can be recycled, limitations and conditions under which the ship recycling facility operates, including as regards hazardous waste management, details on the explicit or tacit procedure for the approval of the ship recycling plan by the competent authority, maximum annual ship recycling output, calculated as the sum of the weight of ships expressed in light displacement tons (LDT) that have been recycled in a given year In that facility, date of expiry of inclusion in the European list information is given [7]. LDT means the weight of a ship in tonnes without cargo, fuel, lubricating oil in storage tanks, ballast water, fresh water, feedwater, consumable stores, passengers and crew and their effects and it is the sum of the weight of the hull, structure, machinery, equipment and fittings of the ship [8].
The dangerous goods inventory on the ship is also listed in detail within the framework of the rules determined by The European Parliament and The Council in November 2013 and published in the European Union Official Journal in December 2013. The use of materials containing asbestos, ozone-depleting agents, polychlorinated biphenyls (PCB), perfluorooctane sulfonic acid (PFOS), and anti-fouling compounds and systems in the installations of new ships is prohibited [8].
Examining the published international regulations show that the damages caused by ship recycling to the environment and human health can be better understood over time and the rules determined by the authorities have become more stringent. Starting with the measures taken by the Basel Convention regarding the cross-border transport of dangerous goods, the ongoing work of IMO and ILO within the framework of ship recycling was further expanded within the framework of the Hong Kong Convention. As a result of the parallel decisions taken by The European Parliament and The Council for the Hong Kong Convention to enter into force as soon as possible, the environmental damage of ship recycling has gained even more awareness. The regulations, which differed in the works of the authorities in the past, now seem to have settled under the umbrella of the Hong Kong Convention. The most important follow-up steps in determining the inventory of dangerous materials that can harm the environment and people are to follow up from the inventory of materials used during the building of the ships to the materials carried during the operation of the ship. Equipping and documenting the facilities that will carry out ship recycling in accordance with these rules and inspecting them periodically following this certification is of great importance for both the environment and the health of the employees.
2.2. Ship Dismantling and Recycling / Rastavljanje i recikliranje brodova
Ships are sent for disassembly after completing their economic life, and while some of the parts on the ship are disposed of by various methods, some of them are disassembled for recycling and sent to the places where they will be used again. Ship recycling is a process with a very high economic benefit, and it has both benefits and harms in terms of the environment.
Fu and Wu, investigated the bioaccumulation of PCBs in mullet fish living in the Ann-Ping port and Er-Jen estuary in Taiwan, where ship dismantling and recycling processes are carried out, and in fish farms located near these areas. While the steel and parts of the ships dismantled in the port of Ann-Pigg were recycled here, some devices such as capacitors and transformers were sent to the Er-Jen estuary for recycling. The on-site dismantling of capacitors and transformers for recycling has caused oil leakage from these devices to the environment and as a result, serious pollution in and around the river [9].
Plastic waste left in the environment during ship dismantling break into small pieces in the water and remain in suspension, preventing oxygen transfer. They also directly affect the food chain by accumulating in sea creatures. Reddy et al. investigated the accumulation of plastic fragments in tidal sediments in the Alang-Sosiya region in India, where the world's largest shipbreaking yards are located. The collected plastic pieces were analysed by separating them according to the polymer types, and as a result, 81 mg of small pieces of plastic were detected in one kg of residue [10]. Patel et al., also observed the anthropogenic effects on bacterial communities by taking samples from the waters in the region in different seasons in their study in the same region. They observed relationships between the level of anthropogenic pollutants in the waters of the region and the structure of bacterial communities, due to the impact of shipbreaking activities. As a result of the study, they reported that the bacterial community shifted from gammaproteobacteria to Betaproteobacteria class because of ship-breaking processes [11].
Hiremath et al. made emission estimations of 241 ships of 6 different types (general cargo, bulk carrier, container, oil and chemical tankers, refrigerator, and passenger) that were dismantled at the shipyards in the Alang region between 2011 and 2013. The authors stated that general cargo, bulk carrier, and container ships produce less landfillble waste during dismantling than the other three types of ships. Glass wool emissions from ships were found to be much higher compared to other types of landfill waste, particularly asbestos and asbestos-containing materials. In addition, as a result of the study, the authors stated that if the ship type is known, the cumulative waste that will occur as a result of the recycling of that ship can be estimated with the emission factors given in the study [12].
Neşer et al. investigated the heavy metal pollution levels in the area where the shipbreaking shipyards are in the Aliağa region of Turkey. As a result of the study, the levels of mercury, lead, copper and nickel in the samples taken from this region were found to be above the threshold effect level (under TEL; adverse effects are not expected to occur) and the possible effect level (PEL; sweat effects are expected to occur) and lead, chromium, copper, zinc and nickel deposits are also considered to be heavily polluted according to the sediment quality guidelines (SQG) [13]. Neşer et al. investigated the amounts of polycyclic aromatic hydrocarbons (PAHs) and aliphatic hydrocarbons in the sediment in the Aliağa region between 2009 and 2010. It was observed that these amounts detected in the region were higher when compared to the PAHs and aliphatic hydrocarbon values of other places in the literature. Shipbreaking shipyards, steel works industry and petrochemical complex in the region are shown as the reason for this [14].
Yılmaz et al. investigated the levels of organic and metal contaminants in sediment samples in the Aliağa region. The levels of PAHs, PCBs, and organochlorine pesticides (OCPs), which are harmful to human and environmental health from organic pollutants, were measured. As heavy metal pollutants, Cd, Cr, Cu, Fe, Mn, Ni, Pb, and Zn were detected in the sediment samples. The authors pointed out that the PCB compound materials used in some parts of the ships cause high pollution in the sediment due to their high-temperature stability and electrical conductivity. In addition, toxic levels of Cu, Pb and Zn were detected in sedimentation samples. It is stated in the article that the disassembly and disposal of equipment containing these organic and heavy metal pollutants should be done carefully [15].
Due et al., explained in their study the harmful substances that occur during ship dismantling, in which part of the ship these substances are found, and their harm in terms of human and environmental health. In the study, two dismantling shipyards were examined, and recommendations were made regarding the disposal of harmful substances [16].
Welaya et al., evaluated the ship recycling facilities in Egypt in terms of worker health, environmental safety and economy. In the study, data were collected by interviewing some shipyard managers and academicians, and a model for ship recycling was proposed using the fuzzy logic approach. The authors stated that with this proposed method, profit and internal rate of return can be evaluated. In addition, as a result of the study, it was stated that the shipbreaking shipyard did not affect the labour and transportation prices but affected the infrastructure costs [17].
Hasan et al. investigated the accumulation of trace metals in sea and ground waters in the areas where shipbreaking activities are carried out along the Bay of Bengal in Chittagong, Bangladesh. They stated that seawater is polluted with Fe, Hg, Mn, Al, Pb and Cd metals, while groundwater is polluted with Fe, Pb, Hg, Mn, Al, and As metals at different rates. The authors concluded that when seawater is polluted, groundwater is also affected and polluted [18]. Hasan et al., compared the trace metal levels of the samples taken from the sediments in the region close to the shipbreaking areas in Sitakund Upazilla of Chittagong, Bangladesh, with the recommended values of the uncontaminated sediments. The metal amounts in the samples taken from the waters in the areas where the shipbreaking operations were carried out were higher than the metal levels in the samples taken from the Sandwip and Karnafully River mouths, which were determined as the study area. While the most polluted metals in the samples were Cr, Zn, As, and Cd, the metals with moderate pollution were Fe, Mn, and Co, and the metal with low pollution was Ni [19].
Hossain et al., examined the effects of shipbreaking activities on the Bangladesh coastline and made recommendations for a sustainable management system. To minimize the damage to the environment, shipbreaking activities should be carried out in an isolated area in the coastal area, regulations should be established for the on-site and off-site disposal of hazardous waste resulting from ship-breaking operations, and to prevent the discharge of oils and metals into seawater and the environment, various penalties must be applied to the environmental protection rules for inclusion. As a result of the study, it was also emphasized that women and children should not work in shipbreaking and transportation of heavy metals and that personal protective materials should be provided to workers by employers [20].
Ko and Gantner examined the life cycle assessment (LCA) of a ship in their study and examined the local added value and environmental effects of scrapping the ship. In the study, LCA, local value added, and eco-efficiency methods were used to quantify the economic and environmental impacts. In the study, it is stated that most of the economic benefits of the ship are to the European owners during the use phase, while the Asian producers are the ones who are exposed to the environmental impact during the production and recycling phase. According to the findings of the study, it is emphasized that shipowners can reduce environmental impacts by investing in technologies used in the production and shipbreaking stages to balance the economic and environmental impact factors [21].
Rahman et al. carried out a detailed life cycle assessment of steel in the ship recycling industry in Bangladesh. The amount of energy consumed during the production of rebar obtained from ship scrap and newly produced rebar and the number of emissions during production were compared. It has been determined that the amount of energy and emissions per ton of rebar produced from ship scrap is much less. It has been stated that the production of primary rebar causes about six times more damage to the ecosystem. In addition, as a result of the study, the authors stated that the changes to be made in the cutting method and the protective equipment used during the cutting will bring benefits to the environment and human health [22].
In the first of two studies examining shipyard processes from a life-cycle perspective, the environmental impacts of steel shipbuilding and recycling were evaluated. The study concluded that the shipbuilding process accounts for 85% of the total impacts, and the life cycle assessment method is recommended as an important approach in the evaluation of shipyard processes [23]. In the second study, the environmental impacts of the shipyard processes for yachts made of aluminium and steel were evaluated from a life cycle perspective. For this purpose, scenarios involving different amounts of aluminium and steel have been developed and it has been observed that environmental impacts increase in parallel with the increase in aluminium use in general [24].
Ship recycling includes mainly ferrous scrap parts and machinery parts. When recycling processes are analysed in terms of cost, it is seen that safety regulations take the first place with a share of 50%, followed by labour costs. While the paint and lead-based batteries released during ship dismantling are seen to be the ship parts that contribute the most to global warming, steel and brass elements are generally considered the most environmentally risky parts [25].
When the studies are evaluated in general, it is revealed that ship dismantling processes are risky in terms of both human health and the environment. Dismantling shipyards in Bangladesh, where ship dismantling is carried out intensively, take the lead in the works. Despite the various and serious harms, it seems that shipbreaking as the first stage of recycling can provide great environmental benefits in the long run. On the other hand, it was strongly emphasized that the protection of workers working in this sector should be emphasized separately.
2.3. Shipyard-Environment Interaction / Interakcija brodogradilišta i okoliša
Shipyards, as heavy industry facilities, can generate large amounts of pollutants. When shipyard processes are examined from the perspective of a ship's life cycle (see Fig. 1), it is seen that they have significant environmental impacts. One of the most emphasized pollutants in shipyard processes is paint emissions. In addition, blasting and welding processes are also examined.
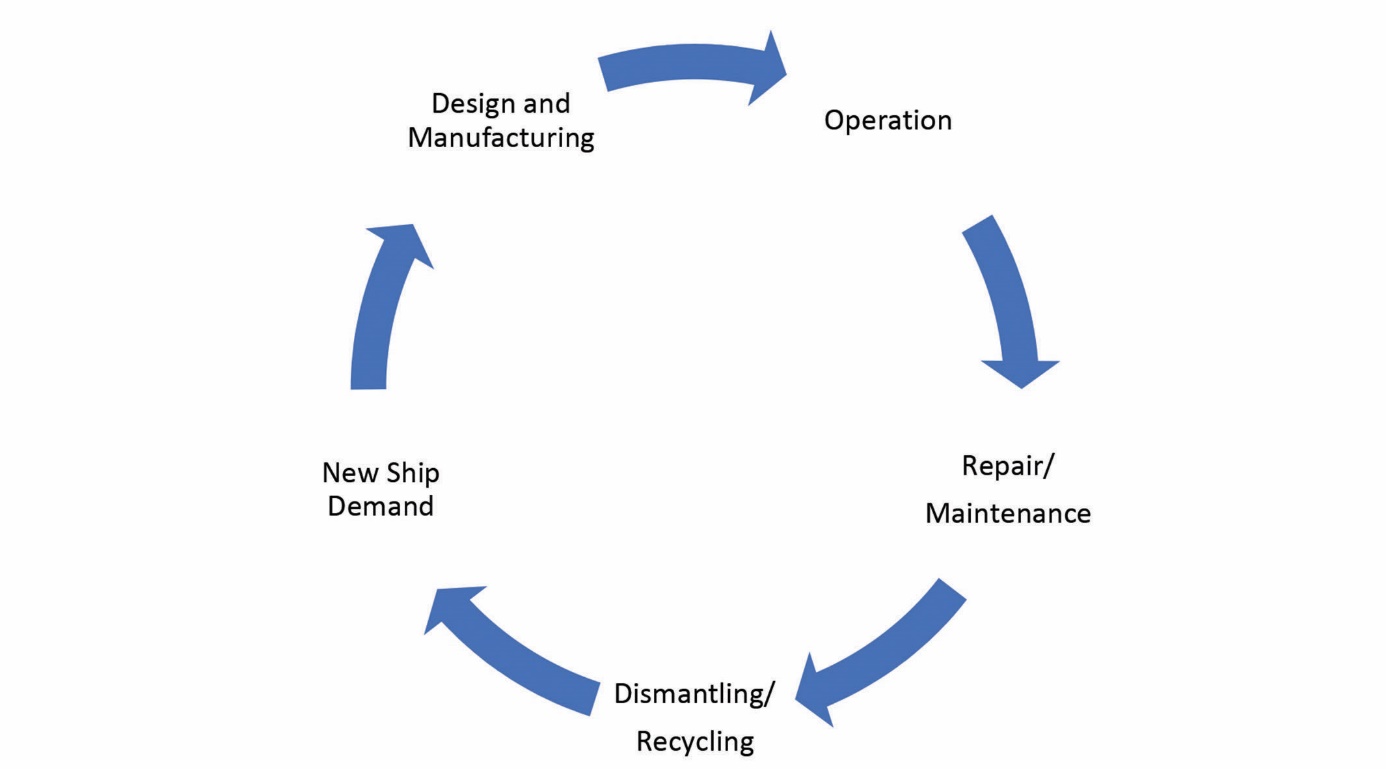
Figure 1The life cycle of a ship
Slika 1. Životni ciklus broda
In a comprehensive study on volatile organic compounds (VOCs) of the painting process in 2007, when no regulation was made on paint emissions, it was determined that the amount of emission was dependent on the painted surface and paint type, and it was observed that paint emissions could be dispersed up to 5 km [26]. In a similar study conducted in 2008, VOC emissions during painting a general cargo ship with a 3500 deadweight (DWT) oil/chemical tanker built in a Turkish shipyard were investigated. According to the proposed mathematical model, VOC emissions depend mainly on the weight of paint per unit surface. Based on these two sample ships, the study concluded that 3,200 tons of VOC emissions were produced in 2010 at Turkish shipyards in Tuzla [27]. In another study, in which the proposed method was applied in this study, it was revealed that much more VOCs are produced in new shipbuilding than in the maintenance/repair process. Calculations for a dry cargo ship show that 17,075 tons of VOCs are produced during shipbuilding and 1,355 tons during maintenance/repair [28].
In a compilation of studies on the elimination of tributyltin (TBT), the base material of antifouling paints, used to solve the problem of fouling, which is one of the most important problems faced by ships and which causes a serious increase in fuel consumption by increasing ship resistance, it is found that this substance is used in large quantities in shipyards. It was pointed out that TBT, which was removed from the surface by blasting, was disposed of with the landfill method as a suitable solution. It was also stated that the preferability of thermal and electrochemical treatments is low due to high investment and operating costs [29]. In a study conducted at a small marina near a shipyard in Busan, Korea, it was found to be contaminated with TBT, Cu, and Zn [30]. Another toxic pollutant, dichlorodiphenyltrichloroethanes (DDT), is detected in shipyards rather than paint factories [31]. In another study, these findings were confirmed and it was stated that the shipyards were contaminated with this dangerous substance [32].
In a study examining the environmental effects of blasting applied for the preparation of the ship surface for the painting process, the emission factors in the case of separate blasting for rusty and painted surfaces were calculated and it was seen that a much larger amount of blasting should be used for the preparation of rusty surfaces [33]. In a study on the welding process, in the measurements made for different electrode types (rutile, basic, and cellulosic), C, Mn, Si, P, and S elements were found intensely in the welding fume [34]. In a similar study, total suspended particles (TSP) production for a 7,100 DWT chemical tanker and a 26,200 DWT container ship was measured as 1.92 t and 2.14 t, respectively [35].
A study on brominated flame retardants (BFRs), another important pollutant, concluded that these pollutants are produced in significant quantities in shipyards and should be evaluated in more detail by the Hong Kong Convention [36]. Metal deposits originating from shipyard processes (paint, fuel, and welding, etc.) accumulate in the soil, especially in the area close to water, and then mix with the water. In a study carried out in Brazilian shipyards, Cr, Ni, Pb, V, and Zn precipitates were found, especially Cu [37]. In a similar study conducted for Brazilian shipyards, it was determined that Cr, Ni, and Zn elements, especially Cu, formed precipitates and that their main source was antifouling dyes, and it was stated that these precipitates had very negative effects on the health of sea creatures living on the coast [38].
Exposure of workers working in processes in shipyards to harmful emissions is an important issue that has been well studied. In a 2003 study, it was found that dye workers were exposed to genetically mutated pollutants and that, besides PAHs, various genotoxic aromatic compounds were also inhaled by workers in significant amounts [39]. In a study conducted on heavy metal exposure in the cutting process in shipbreaking yards, it was determined that the heavy metals released spread up to 245 meters away and up to 9.33 m in certain conditions, and the Pb concentration reached 8-30 µg/Nm3 in the central region. This value is well above the 0.5 µg/Nm3 limit set by India [40]. In a study investigating the effect of welding emissions on the sleep patterns of welders and office workers working in shipyards, the amount of PM2.5 exposed to office workers was measured to be 82.1±94.1 µg/m3, while welding workers are exposed to 2166.5±3149.1 µg/m3 emissions. In addition, the emissions of Cu, Mn, Co, Ni, Cd, and Pb to which welders are exposed are also associated with hormones that cause sleep disturbance [41]. In another study approaching the subject of exposure from a different perspective, the sensitivity of workers to noise was examined and it was stated that the daily noise exposure of the workers working in the cutting process exceeded the specified standards, which could cause permanent hearing loss in the long run [42].
3. DISCUSSIONS AND CONCLUSION / Rasprava i zaključak
Shipyards are heavy industry facilities and each process in the shipyards may pose great environmental risks. Among shipyard processes, especially painting has the potential to cause serious damage not only in the shipyard but also around the shipyard. It is important to examine the effects of respirable particles on shipyard workers and people around the shipyard. Among the environmental impacts caused by the shipyards, especially those on human health, can be revealed by the studies to be carried out in cooperation with the hospitals operating around the shipyard or in the regions where the shipyard workers reside. In addition, examining the effects of shipyard waste on aquatic life is also important for the evaluation of environmental impacts. Especially in the areas where the shipyards are densely located, the coasts may be contaminated with large amounts of particulate pollutants and heavy metals. The examination of sediment samples to be taken from these regions will be an example for further studies for the accurate determination of shipyard pollution.
Another form of ship-related pollution occurs during the recycling of ships that have completed their lifetime. Although this process is important for the use and reuse of steel and other equipment from ships in other sectors, ships may cause many harmful particles to spread to the environment during dismantling due to the load they carry and the equipment they contain during operation. Ships should be in the process of continuous inspection not only when they are going to be recycled, but also in the processes from construction to operation and repair maintenance as if they are going to be recycled at any time. In this way, the inventory of hazardous materials that may harm the environment and human beings can be determined and appropriate procedures can be applied for the disposal of these materials. Therefore, shipyards and ship operators engaged in dismantling should be subject to a strict procedure by international legislation. Starting with the measures taken by the Basel Convention regarding the cross-border transport of dangerous goods, the ongoing work of IMO and ILO within the framework of ship recycling was further expanded within the framework of the Hong Kong Convention. As a result of the parallel decisions taken by The European Parliament and The Council for the Hong Kong Convention to enter into force as soon as possible, the environmental damage of ship recycling has gained even more awareness. The effective implementation of these regulations in third-world countries where ship recycling is most affected is of great importance in terms of the environment and human health.
Shipyard-related environmental pollution is a major problem when there are populated cities in the vicinity of the regions where shipyards are densely located (see Istanbul example). The environmental problems caused by shipyard processes have been relatively well studied, but it is clear that a holistic approach is needed. It should be recognised that the environmental problems caused by shipyards are not only caused by the shipyard processes but also by the materials and energy demanded by the shipyards. Therefore, to fully understand the extent of shipyard-related environmental pollution, it is suggested that the life cycle perspective should be used in a more detailed and comprehensive manner and a guideline like the 'Guidelines on Life Cycle GHG Intensity of Marine Fuels (LCA Guidelines)' that IMO is currently working on should be established.
Author Contributions: V.Ş. and L.B.; Methodology, Literature Investigation, Writing – Original Draft, Writing – Review & Editing
Funding: The research presented in the manuscript did not receive any external funding.
Conflict of interest: None